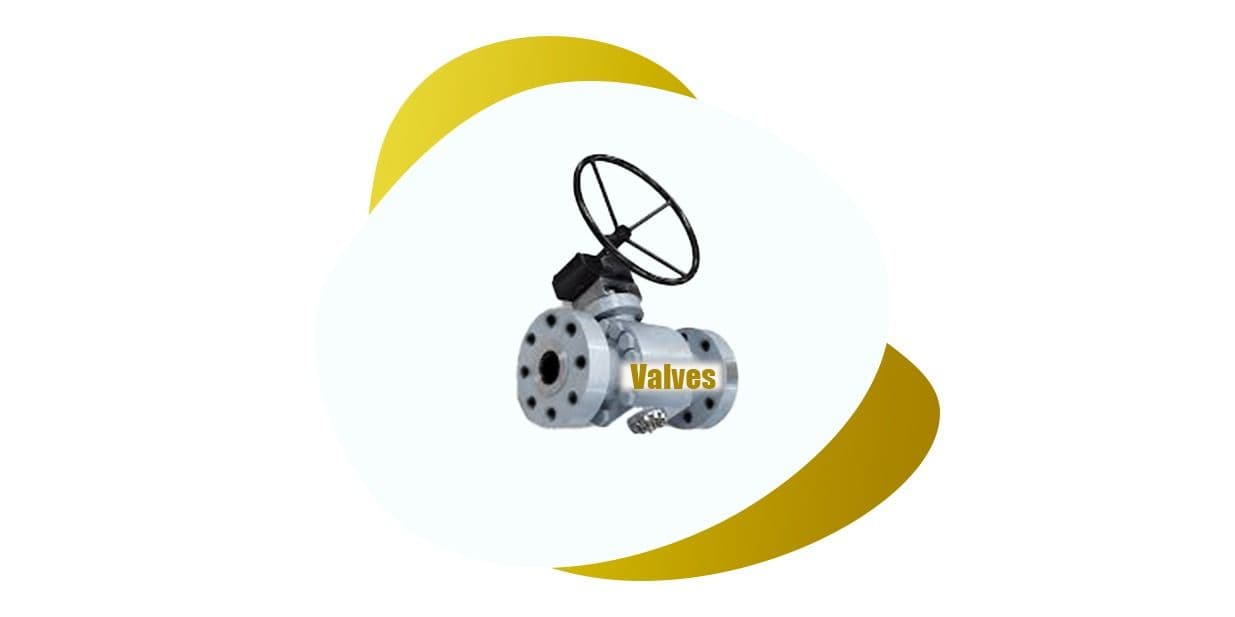
Valves
Description of Valves
- Valves are essential mechanical components designed to control or regulate the movement of liquids, gases, or slurries in a system. By opening, closing, or partially blocking passageways, valves manage the flow, pressure, and direction of movement within a system. Many industries, such as oil and gas, water treatment, pharmaceuticals, and power generation, rely on valves to maintain safety and efficiency in their operations.
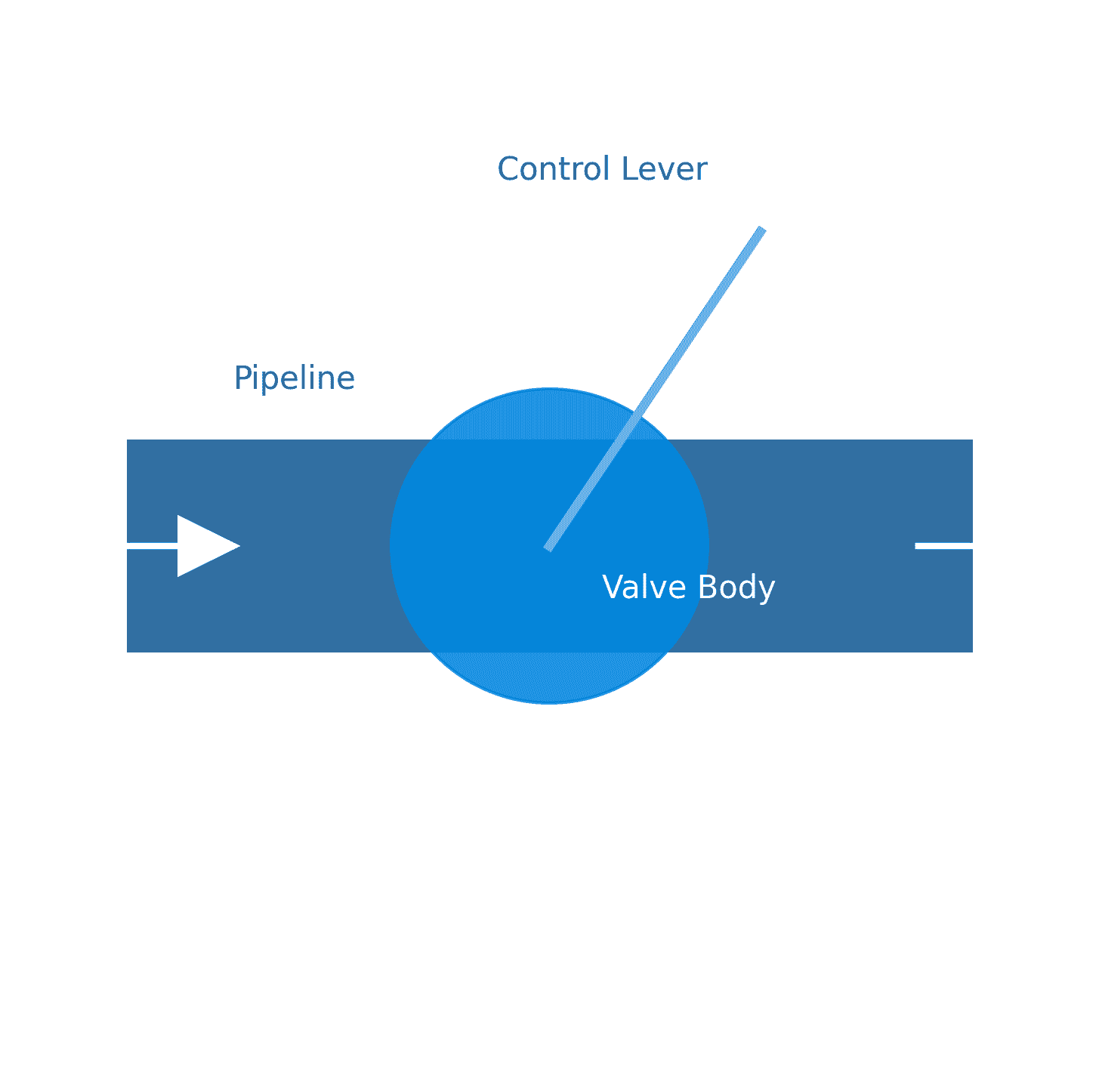
Importance of Valves
Imagine a world without valves—water distribution would be completely uncontrollable, industrial processes would be highly inefficient, and safety protocols would be grossly inadequate. Valves play a critical role in fluid mechanics and system control, enhancing effectiveness and ensuring safety across multiple industries. Without valves, water supply systems in homes, cities, and industries would be chaotic, leading to massive waste, frequent pipeline failures, and uncontrollable floods. Imagine trying to regulate water flow in a municipal system without valves—there would be no way to stop leaks, control pressure, or isolate sections of the pipeline for maintenance, resulting in extensive water loss and infrastructure damage.
Similarly, in industrial processes, valves are indispensable for controlling the movement of gases, liquids, and even semi-solid materials. Industries such as oil and gas, chemical manufacturing, power generation, and food processing rely heavily on valves to regulate flow rates, maintain pressure, and ensure precise control over production processes. Without valves, reactors, boilers, and storage tanks would be prone to dangerous pressure build-ups, potentially leading to catastrophic failures, explosions, or hazardous spills. The absence of valves in these industries would not only reduce efficiency but also pose severe risks to both workers and the environment.
Furthermore, valves play a significant role in safety mechanisms, preventing accidents and equipment malfunctions. In nuclear power plants, for instance, specialized control valves are crucial in managing coolant flow, preventing overheating, and ensuring stable reactor operations. Without properly functioning valves, nuclear plants would be unable to regulate temperatures effectively, increasing the risk of meltdowns and radiation leaks. In the healthcare industry, valves in medical devices such as ventilators, infusion pumps, and anesthesia machines ensure that patients receive precise amounts of air, fluids, and medication. A world without valves would make modern medical treatments unreliable and dangerous, severely affecting patient care and survival rates.
Transportation systems, including automobiles, airplanes, and ships, also depend on valves for engine efficiency, braking systems, and fuel flow regulation. The absence of valves in these systems would result in poor performance, frequent mechanical failures, and heightened safety risks for passengers and operators. Even in everyday household applications, from washing machines to dishwashers and heating systems, valves provide control and convenience that most people take for granted.
Ultimately, valves are the unsung heroes of modern infrastructure, technology, and industry. Their presence ensures precision, efficiency, and safety, making them indispensable across various fields. Without valves, our world would be plagued by inefficiency, danger, and chaos, underscoring their critical importance in both everyday life and large-scale industrial operations.
Different Types of Valves and Their Uses
Various types of valves exist for specific applications. Below is an overview of the most common types:
1. Gate Valves
Gate valves are primarily used to allow or stop the flow of liquids. When fully open, they offer no resistance, making them ideal where unrestricted flow is required. However, they are not designed for flow regulation.
Common Applications:
- Municipal water supply systems
- Oil and gas transportation
- Power plants
2. Ball Valves
Ball valves control fluid flow using a rotating ball with a hole in the center. These valves are highly durable, reliable, and provide an effective shut-off mechanism.
Common Applications:
- Petroleum and natural gas industries
- Water purification plants
- HVAC systems
3. Butterfly Valves
Butterfly valves are cost-effective, lightweight, and suitable for large pipe sizes. They regulate flow through a rotating disc.
Common Applications:
- Chemical production
- Food and beverage industry
- Municipal water supply systems
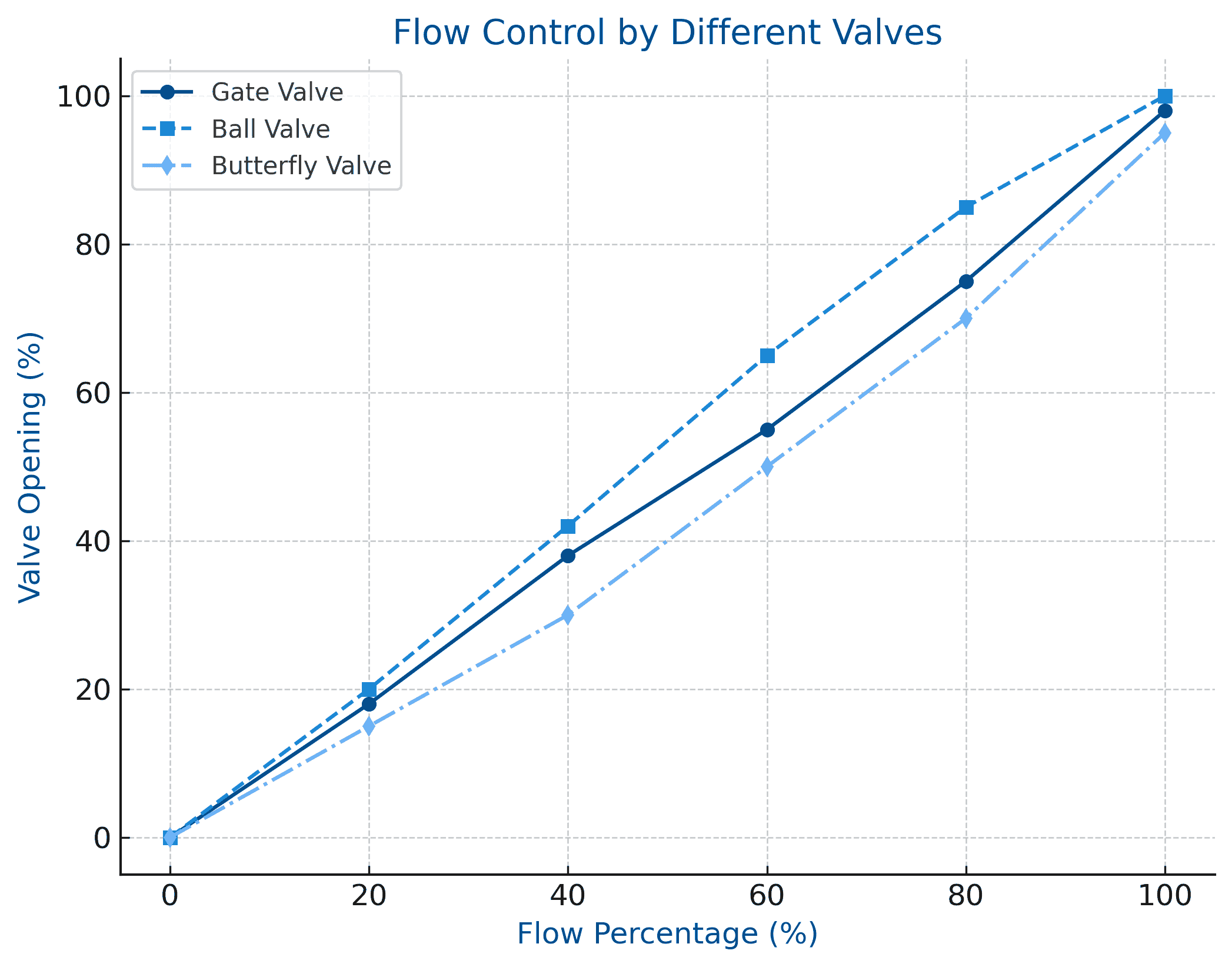
4. Check Valves
Also known as one-way valves, check valves prevent fluid from flowing backward in a pipeline, ensuring unidirectional movement.
Common Applications:
- Water and fluid pumping stations
- HVAC installations
- Wastewater management systems
5. Globe Valves
Globe valves use a movable plug to regulate the flow of specific fluids. These valves are ideal for applications requiring precise flow adjustments.
Common Applications:
- Steam distribution networks
- Fuel oil systems
- Industrial cooling processes
6. Diaphragm Valves
Diaphragm valves are ideal for handling high-purity or corrosive fluids. They use a flexible diaphragm to regulate flow.
Common Applications:
- Pharmaceutical manufacturing
- Food and beverage production
- Water treatment plants
7. Needle Valves
Needle valves provide highly precise flow control through a narrow, tapered stem.
Common Applications:
- Laboratory equipment
- Hydraulic machinery
- Gas flow measurement instruments
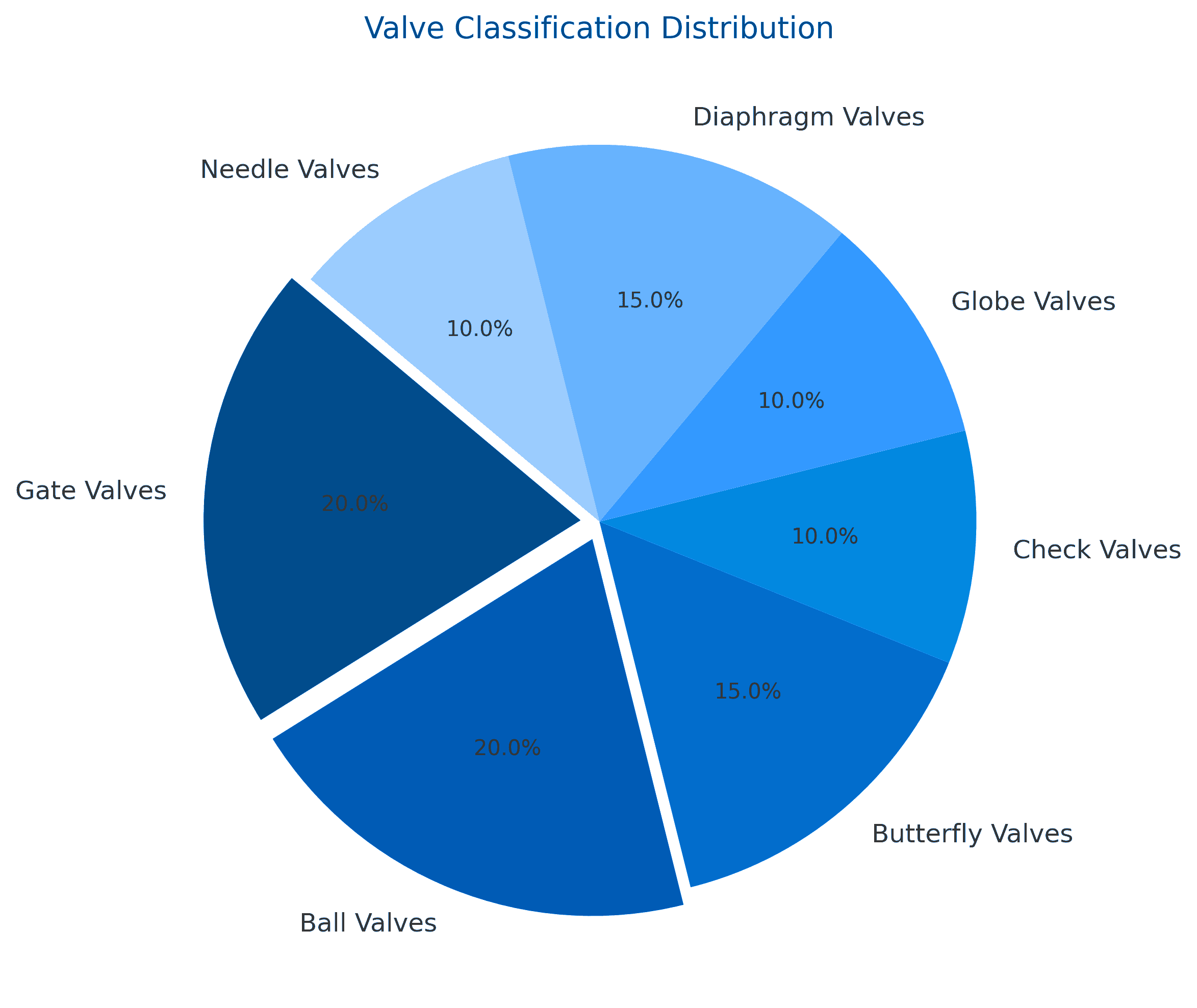
Choosing the Correct Valve
Selecting the appropriate valve depends on several factors:
- Type of Fluid: Different valves are designed for liquids, gases, or slurries.
- Pressure Limits: High-pressure applications require robust valves.
- Temperature Tolerance: Valves must withstand extreme temperatures when necessary.
- Industry-Specific Requirements: Various industries have unique specifications for valve design and function.
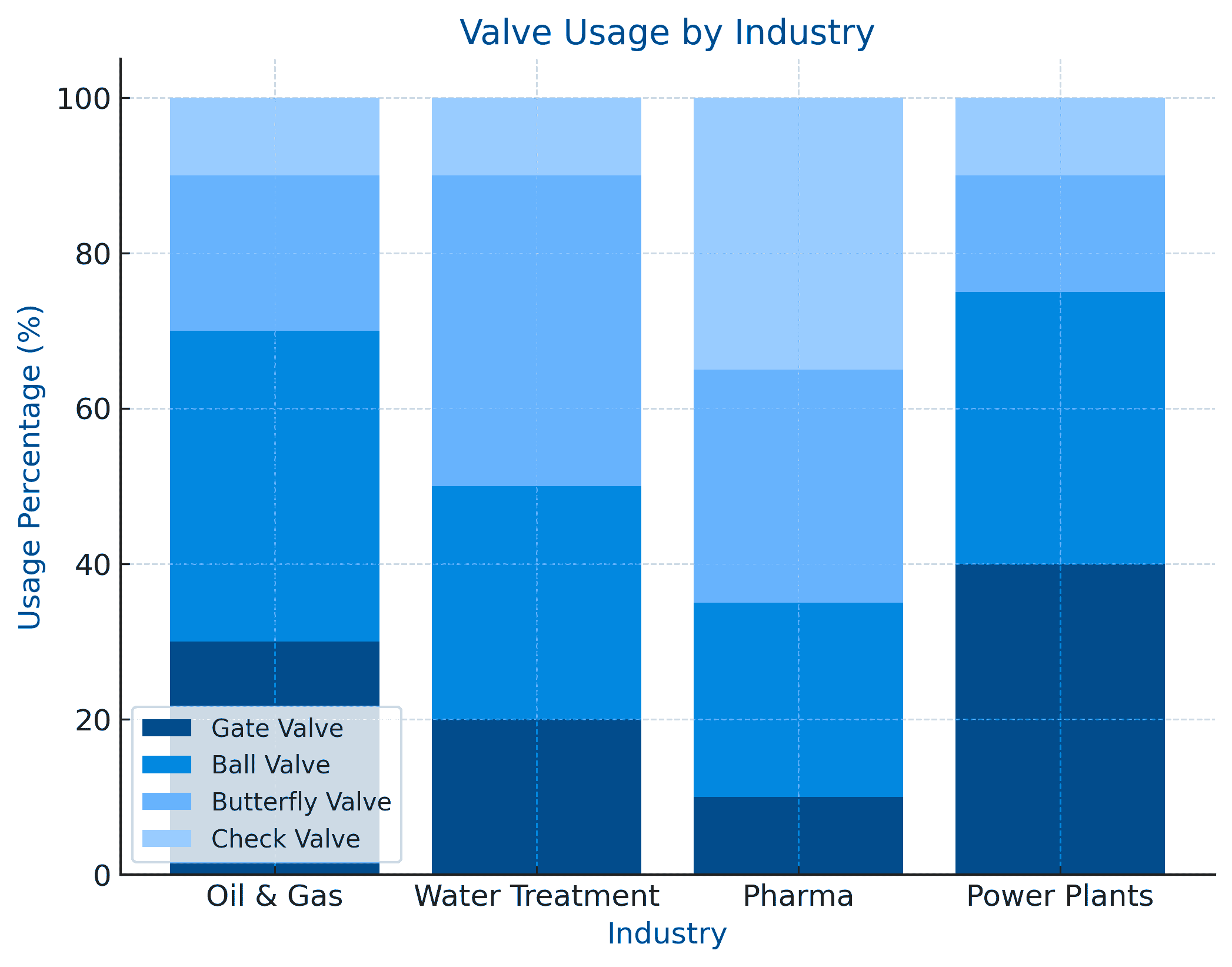
Survey Note: Detailed Analysis of Valves in Energy and Water Conservation
Valves, often underappreciated in discussions of sustainability, are critical devices that regulate the flow of fluids such as water, steam, and gases in residential, commercial, and industrial settings. This survey note explores their role in enhancing energy efficiency and water conservation, drawing on extensive research and data from renowned organizations like the U.S. Environmental Protection Agency (EPA), the U.S. Department of Energy (DOE), and industry reports. The analysis aims to provide a comprehensive understanding for stakeholders seeking to optimize resource use, with a focus on practical applications and quantifiable benefits.
Valves and Water Conservation: Mechanisms and Data
Water conservation is a global priority, and valves play a significant role by controlling flow to minimize waste. Several valve types and applications contribute to this effort:
- Flow Limiting Valves: These valves maintain a fixed, pre-set flow rate regardless of pressure fluctuations, reducing water consumption. For example, automatic flow limiting (AFL) valves are used in showers, wash basins, and appliances like washing machines, aligning with UK government recommendations of 6 liters per minute for hand washing and 9 liters per minute for showers (Conservation Valves).
- Water-Saving Flush Valves: In commercial restrooms, these valves reduce water per flush, with high-efficiency models saving significant volumes. For instance, upgrading to dual-flushing valves can reduce water use by up to 30% compared to traditional models (Water Saving Flush Valves).
- Efficient Faucets and Aerators: The EPA’s WaterSense program labels faucets with a maximum flow rate of 1.5 gallons per minute (gpm), compared to standard models at 2.2–2.5 gpm. Research suggests that replacing old faucets with WaterSense-labeled models can save up to 700 gallons of water per year per family, based on average use (Water-Efficient Faucets). Additionally, low-flow aerators can save over 60 billion gallons annually if installed nationwide, according to Conservation Mart (Water Saving Faucet Aerators).
- Pre-Rinse Spray Valves: In commercial kitchens, replacing inefficient pre-rinse spray valves (flowing at 1.6 gpm or more) with high-efficiency models can save over 7,000 gallons per valve per year, as noted by the EPA. This also reduces natural gas use by over 5,700 cubic feet annually due to lower hot water demand (Pre-Rinse Spray Valves).
These examples illustrate how valves directly reduce water consumption, with additional energy savings from decreased heating and treatment needs. The EPA’s initiatives, such as WaterSense, provide benchmarks and incentives, making these upgrades accessible and cost-effective.
Valves and Energy Efficiency: Technical Insights and Savings
Energy efficiency is closely tied to valve performance, particularly in systems where fluid flow impacts power consumption. Valves contribute to energy savings by optimizing flow control, minimizing losses, and reducing operational costs:
- HVAC Systems: In heating, ventilation, and air conditioning, valves like differential pressure control valves (DPCVs) and pressure independent control valves (PICVs) ensure correct flow rates and maintain delta-T (temperature difference), crucial for boiler and chiller efficiency. Hattersley notes that proper valve selection impacts pump running costs and boiler efficiency, especially for condensing boilers where return water temperature is key (Energy Efficiency in HVAC). The Belimo Energy Valve, for instance, monitors coil performance and optimizes heat exchange, potentially saving significant energy in large buildings (Belimo Energy Valve).
- Power Plants and Industrial Processes: Valves regulate steam and water flow in power generation, directly affecting turbine efficiency. Valmet highlights field-proven valve solutions that increase turbine capacity by up to 75% with new technologies, crucial for bioenergy and waste-to-energy plants (Valves for Energy Industry). In industrial settings, efficient valve selection reduces pressure drops, lowering energy needs for pumping. The DOE’s Pumping System Assessment Tool (PSAT) helps estimate energy losses from throttled valves, with low-loss options like butterfly valves (K=0.5–2) saving energy compared to high-loss globe valves (K=3–8) (Energy Savings Opportunities).
- Solenoid and Pneumatic Valves: Modern designs, such as low-energy solenoid valves, consume less power (e.g., 6 Watts historically reduced through material and design changes), improving electrical efficiency in automation systems (Pneumatic Valves Efficiency).
The DOE’s resources, including the 2006 “Improving Pumping System Performance: A Sourcebook for Industry,” provide detailed guidance on valve-related energy savings, emphasizing the importance of proper sizing and maintenance (DOE Pumping Systems).
Conclusion
Valves are critical components in fluid control systems across multiple industries, playing a crucial role in regulating the flow of liquids, gases, and even semi-solids. The type and function of a valve determine its suitability for specific applications, ensuring seamless operation in various sectors such as water distribution, oil and gas, chemical processing, power generation, and healthcare. From managing municipal water supply networks to controlling gas pressure in industrial plants, proper valve selection enhances safety, efficiency, and durability.
Different types of valves, including gate valves, ball valves, butterfly valves, and check valves, serve unique purposes. For instance, gate valves provide full flow control in pipelines, while ball valves offer quick shutoff capabilities. Butterfly valves are ideal for large-scale flow regulation, whereas check valves prevent backflow, protecting system integrity. By choosing the right valve, industries can optimize performance, minimize operational risks, and extend equipment lifespan.
However, selecting a valve is not just about function; it must comply with industry standards, material compatibility, and pressure requirements. Valves should be tested and certified to meet safety regulations, ensuring reliable performance under varying conditions. Proper valve selection, installation, and maintenance are essential for achieving long-term efficiency and operational success.
Frequently Asked Questions
1. What is the most commonly used valve?
Ball valves are among the most widely used due to their durability, long service life, and excellent sealing properties.
2. How does a gate valve differ from a ball valve?
Gate valves use a gate mechanism to control water flow, whereas ball valves use a rotating ball with a hole. Ball valves offer superior sealing, while gate valves are better for applications requiring full open or closed positions.
3. Can valves regulate pressure?
Yes, certain valves, such as pressure relief valves and globe valves, help manage system pressure effectively.
4. Are valves only manually operated, or can they be automated?
Valves can be manual, automatic, or remotely controlled using electric, pneumatic, or hydraulic power sources.
5. What maintenance practices help maximize valve performance?
Regular inspection, lubrication, and cleaning are essential for extending valve life. Proper installation and operation within specified limits also contribute to longevity and efficiency.