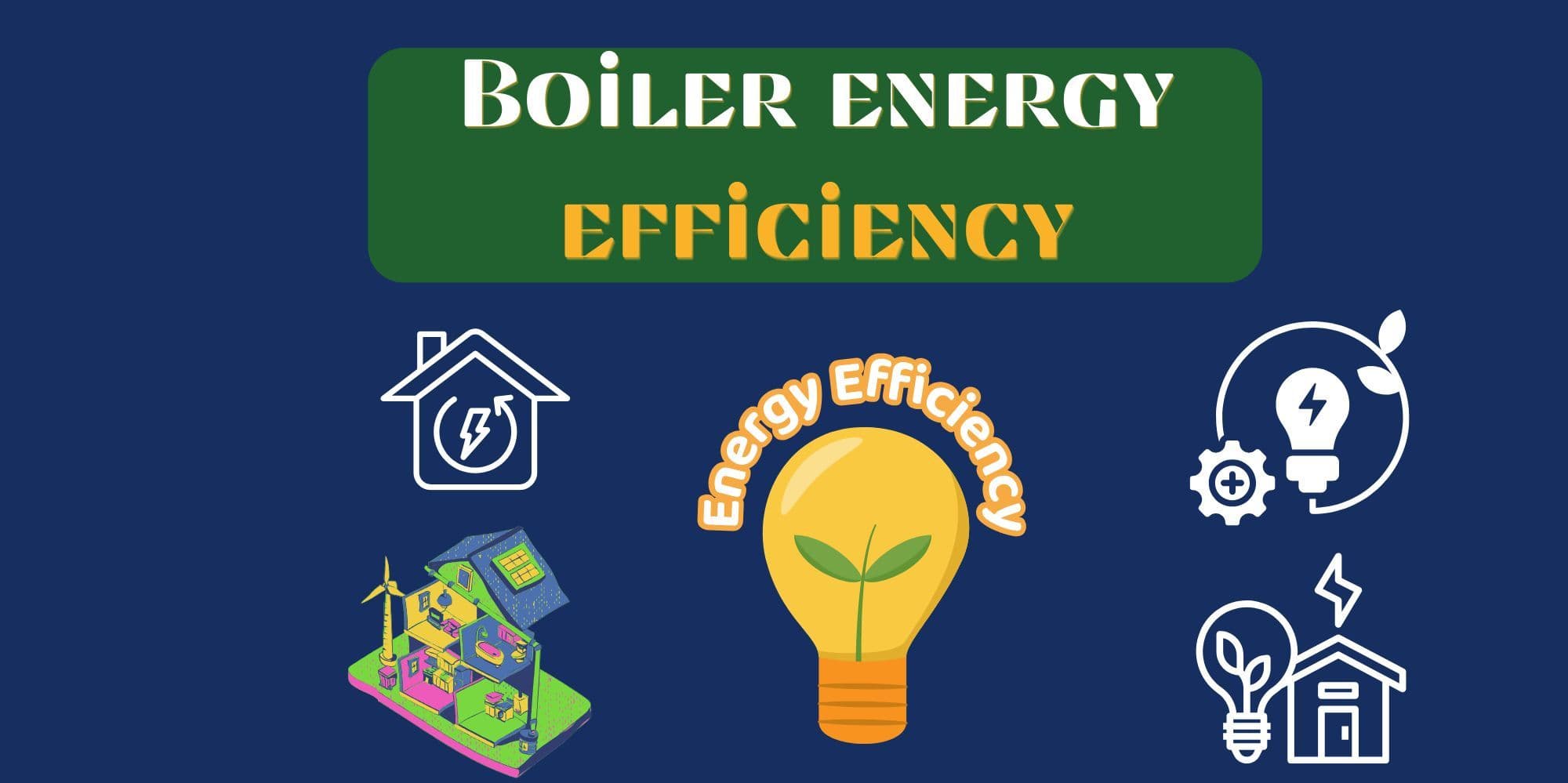
Boiler Efficiency Improvement Guide
Introduction
Is Your Boiler Spending Energy Costs Silently?
Did you know an inefficient boiler system can remain stealthy while increasing your energy expenses and not delivering value at the same time? Efficiency and performance, as well as overall fuel savings, are very important for both residential heating systems and industrial boiler setups. An ineffective system leads to energy wastage, increased maintenance costs, and environmental damage.
In this ultimate guide. expert advice, case studies, and researched approaches have been used to analyze maximized techniques to attaining boiler efficiency. Learn the appropriate methods of maintenance, fuel, and advanced technology and their impacts for maximum cost efficiency and environmental practices.
Understanding Boiler Efficiency
a. What Is Boiler Efficiency?
Efficiency measures the ratio between usable output and input of heat within a system. Usable fuel heat produced by the boiler is considered its efficiency. Bigger efficiency translates to lower energy requirements and reduced running costs.
b. Why is Boiler Efficiency Important?
A more efficient boiler uses less fuel than an already existing boiler of new make, thus lowering the money spent on refilling.
The ecosystem receives fewer harmful emissions, reducing the carbon footprint.
- Enhanced Performance: Prevention of overheating and breakdowns is guaranteed with oscillation-free heating.
- Equipment Life Extrapolation: Boiler system lifespan is efficiently prolonged with proper maintenance. Additionally, maintenance also adds value to equipment life.
c. What Are Some Criteria For Measuring Boiler Efficiency?
- Thermal Efficiency: Ability of converting heat energy into steam or hot water is monitored with this measurement.
- Combustion Efficiency: This measures the degree of fuel burned in the combustion chamber.
- Fuel to Steam Efficiency: This measures the effective transfer of heat into water and its losses in the process.
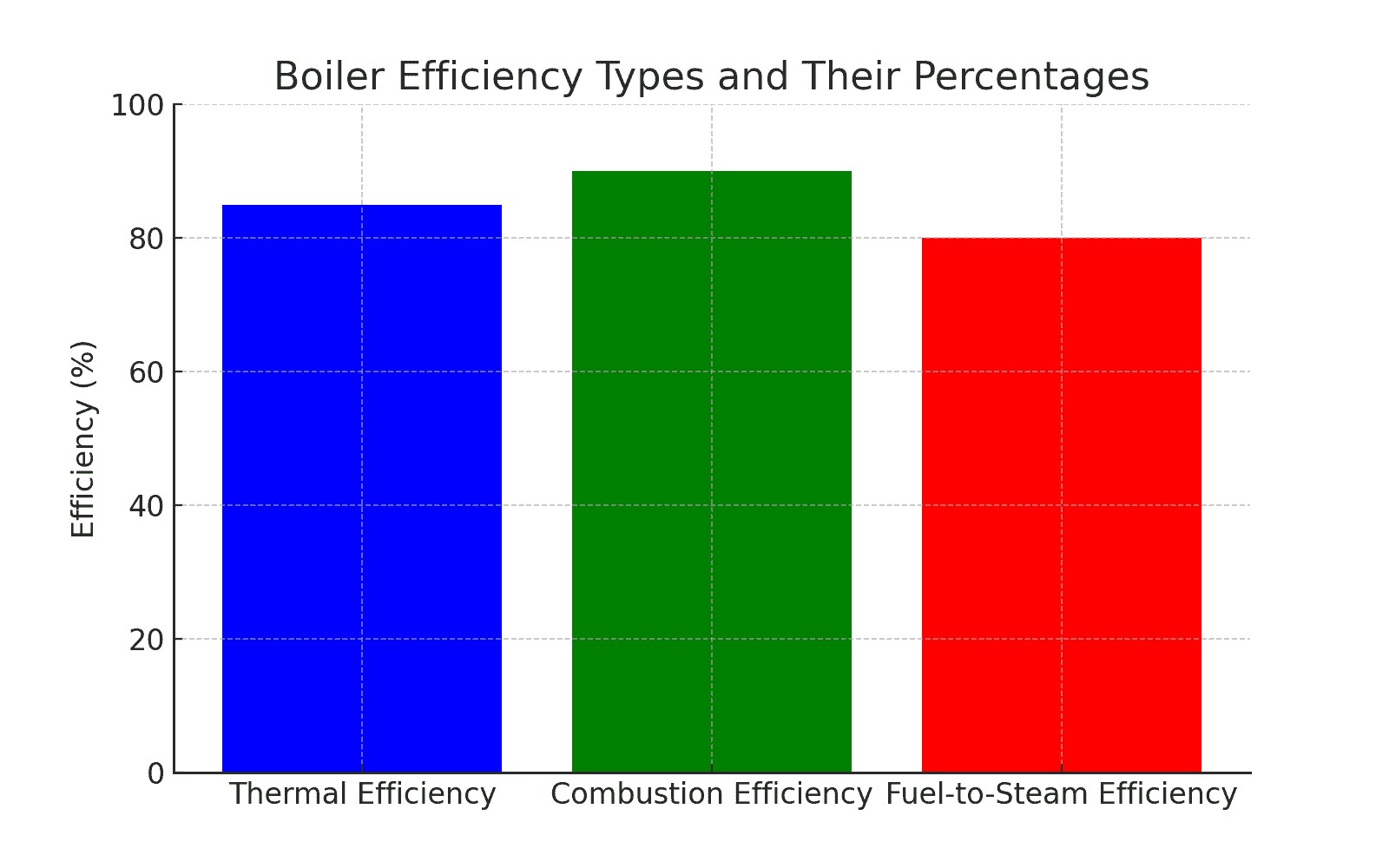
Case Study Example:
XYZ Manufacturing Plant saves thousands each year in fuel costs by improving their boiler’s efficiency to twenty percent.
Ways to Improve Boiler Efficiency
1.Regular Maintenance and Cleaning
Over time, soot and debris accumulate and get stuck inside a boiler, slowing down the burning fuel rate. Careful maintenance will greatly enhance boiler performance.
Importance of Maintenance
- Loss Prevention: Removal of soot and scale deposits will guarantee energy savings.
- Alternatives to Paying For Emergency Repairs: Spending is reduced by addressing minor concerns before they cost too much to fix. Routine inspections allow for early detection.
- Adds value to lifespan: Fewer replacements are required and as a maintained system provides more value.
Critical Tasks
- Wash down and inspect heat exchangers: Correct scaling and soot cleaning.
- Check for Leaks: Check frequently for leaks on the boiler and the pipes because they add to loss in efficiency.
- Control Pressure and Temperature: Comprehensively monitoring the pressure and temperature settings of the boiler ensures steam operating efficiency.
2.Optimizing Combustion Efficiency
Maximum efficacy is achieved at a certain optimal fuel to air ratio for boilers. An excess of air results in heat loss while insufficient amounts produces incomplete combustion leading to sooth stains.
- Certain Combustion Optimizational Strategies:
- Install Trim Systems for making on-spot adjustments to fuel and air ratios.
- Conduct Routine Testing and Adjustments of Burners for standard optimal flame.
- Analyze Flue Gas Emissions to look for signs of inefficient burning.
As an example, ABC Heating Solutions implemented automatic control on fuel and reduced fuel use by 15%.
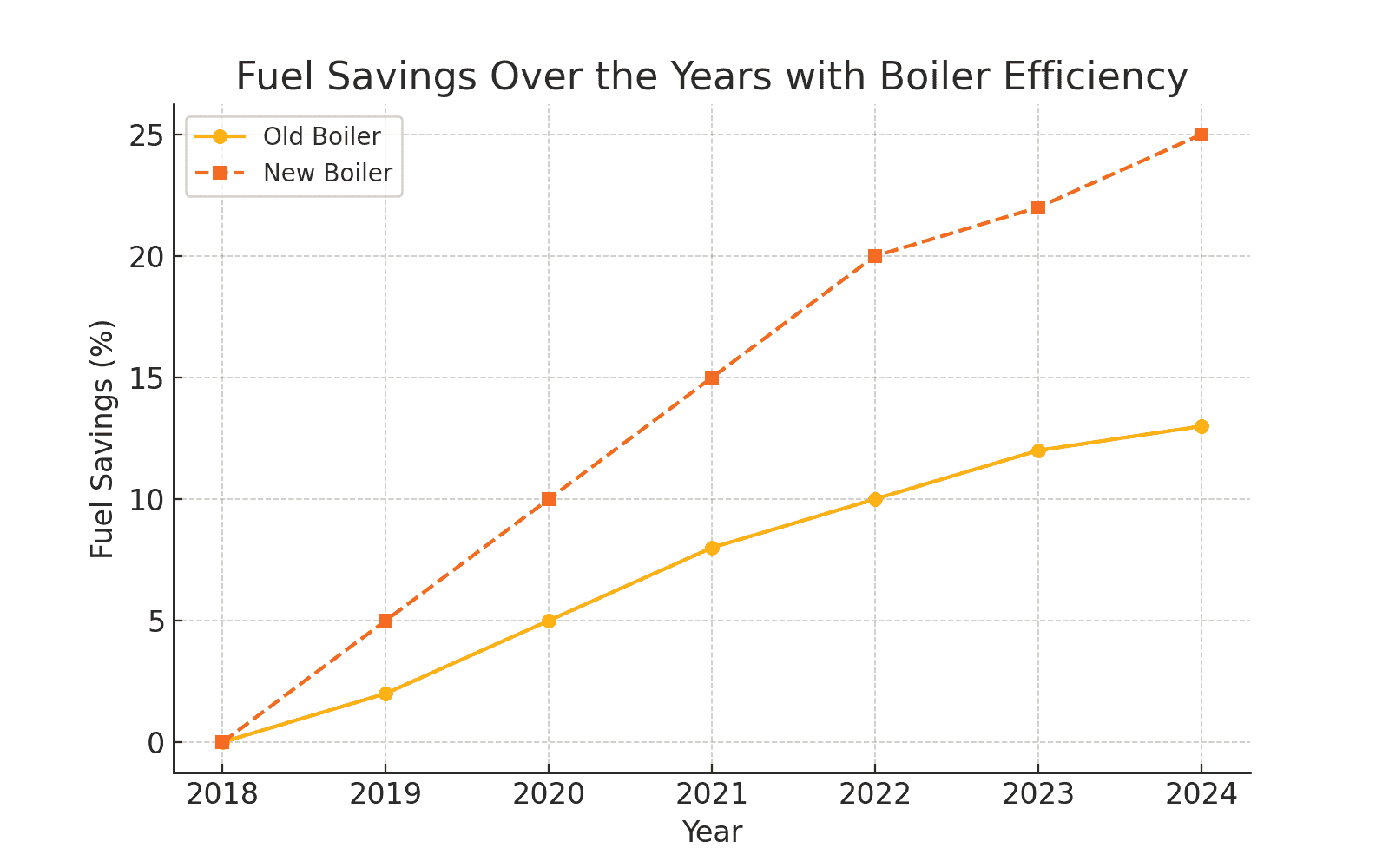
3. Change to a More Efficient Boiler System
Older boilers suffer from continual efficiency losses because of their age. It is recommended to install a condensing boiler as it can reach 98% efficiency by recovering heat that is otherwise released through exhaust gases.
Benefits of Upgrading
- Decreased Fuel Expenses: An increase in energy efficiency results in lower operating costs.
- Less Emissions: New boilers are designed to reduce greenhouse gas emissions.
- Increased Performance: Higher automation and accuracy is achieved through advanced boiler controls.
Example: A case study involving GHI Chemical Plant showed that enhanced water treatment improved maintenance cost by 20% due to heat exchanger efficiency improvements.
4.Enhance Water Treatment
Corrosion and scaling owing to water impurities may significantly impact water efficiency.
Combine Various Methods To Achieve The Best Water Quality:
- Inhibit scale formation: Use Water Softeners.
- For removal of minerals and deposits, use Chemical Treatment.
- Regularly scheduled blowdown also aids in the removal of sludge with minimal impurities.
5.Improve Control of Boiler Load Management
Fuel waste is considerable when a boiler works below fifty percent of its capacity. It is critical to control and monitor the load.
Enhanced Load Management Checklist
- Use techniques that match demand with bait management. These include matching fire to the demand for operation.
- Add a Parallel System with smaller flexible boilers.
- Energy Assessments: Users need to modify through legal standards operative activities that result in suboptimal energy inefficiency.
6.Heat Loss Alleviation without Improving Insulation
The greatest single factor a Boiler system can improve its efficiency remains temperature immersion water heating.
Energy Loss Deficiency Identification
- Inability to Insulate Pipes: Uninsulated pipes allow considerable heat escape along supply pipes to end use locations devoid of insulation.
- Prevention of Boiler Leakage Repairs: Unconstrained boiler leak repair policies lead to energy bypass.
- Heat Efficient Burner Installation: Installation of burners exceeds greatly enhanced heat transfer.
- JKL Energy Solutions improved its insulation structure which increases heating expenditure on cutting expenses by annually 18 percent.
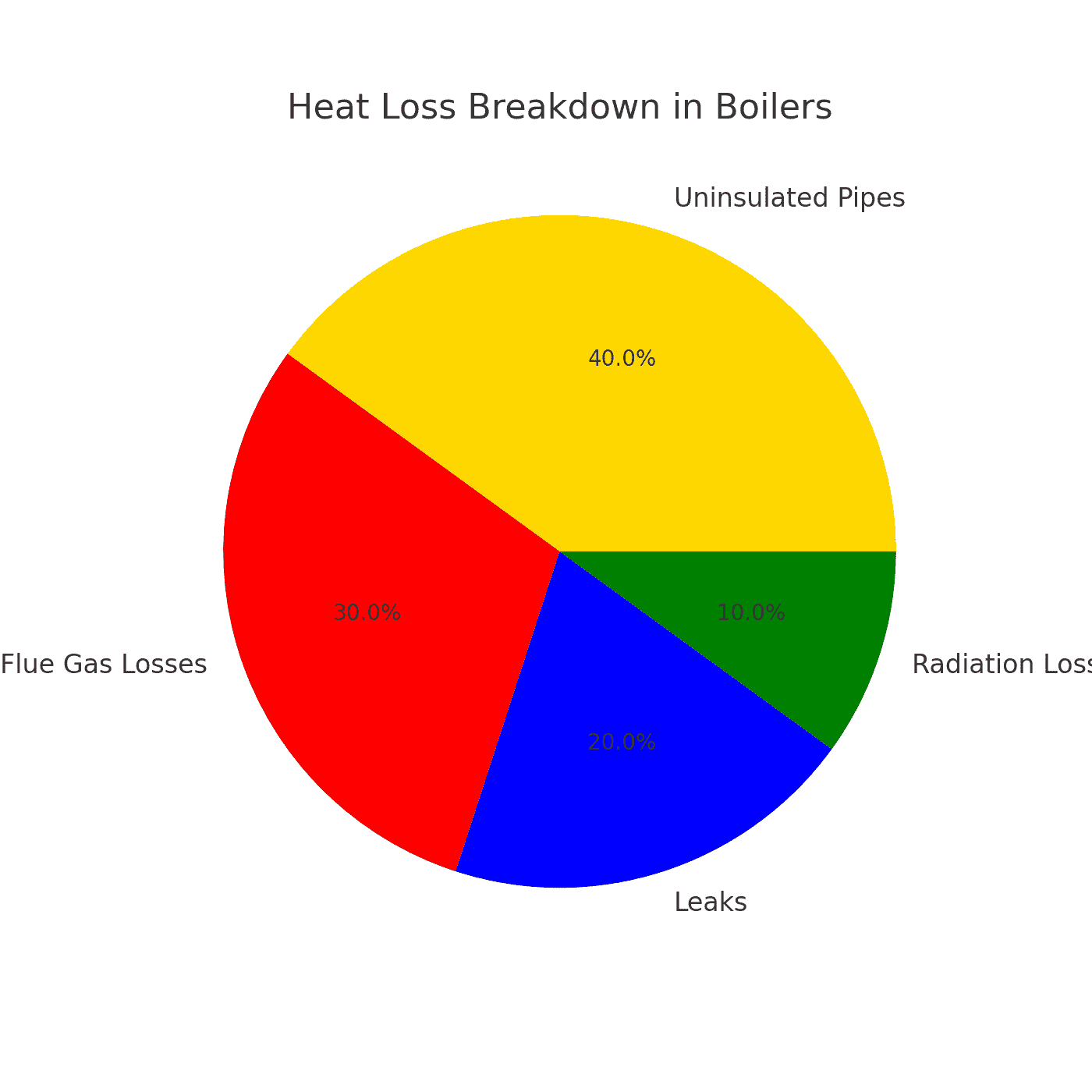
7.Automated Control Optimization
- Research shows experts believe fuel and energy expenditure in their substantive wastage are results of boiler overhaul controls systems adjustments on setting.
- Balanced Control Policies
- Enable tuning temperature and pressure management with digital control devices.
- Boiler Blowdown Automating water use and scaling reduction.
- Set Motors Ratio in Driving Behavior Options of VSD use parameters to change from driving modes with respect to load changes.
8.Form the goal of a defined and limited work scope for each component of the system
- Check and Balance Water Chemistry: capped water supply results leads to hardening supply and mineral deposits forming resulting in system failure through wear.
- Corrosion Inspection is part of the maintenance plan and will be performed as scheduled.
- Flue Gas Analysis and blanking are to be done for assessment of boiler efficiency on a regular basis.
Increase recovery of water from boiler exhaust heat
The boiler's primary exhaust poses significant loss of energy, which if addressed by a heat recovery system, could dramatically improve overall efficiency.
Methods of boilers heat recovery
- Economizers Are used for the additional recovery and reuse of flue gas heat.
- Condensing Heat Exchangers: Also retrieved is latent energy from residual gas which economically offsets the fuel use.
- A primary manufacturing plant has been able to save on average 30% of their fuel expenditure by the adoption of waste heat recovery systems.
Conclusion
Enhanced boiler efficiency is an additional return/profit brought about through reduced energy utilization, emission output, and extending equipment life. It can also be achieved through regular upkeep, prudent selection of fuel, combustion systems, or optimizing heat recovery systems.
Start implementing these methods now if you wish to change your approach to heating in a cost effective window, or if boiler efficiency is low, professional servicing should be done to capture reap benefits on energy spend and eco-friendly initiatives.
Frequently Asked Questions
1. What is the best way to improve boiler efficiency?
The best way to improve boiler efficiency includes regular maintenance, optimizing combustion efficiency, upgrading to a condensing boiler, improving water treatment, and minimizing heat loss through insulation and heat recovery systems.
2. How often should a boiler be serviced?
It is recommended to service a boiler at least once a year to ensure it operates efficiently and safely. Regular inspections help detect leaks, scaling, and inefficiencies before they lead to major issues.
3. What are the signs of an inefficient boiler?
- Increased fuel consumption
- Uneven heating or frequent temperature fluctuations
- Excessive soot buildup
- Frequent repairs and breakdowns
- Visible leaks or pressure loss
4. How does water quality affect boiler efficiency?
Poor water quality can lead to scaling, corrosion, and sludge buildup, reducing heat transfer efficiency and increasing fuel consumption. Using water softeners, chemical treatment, and regular blowdowns can help maintain efficiency.
5. What is the difference between thermal efficiency and combustion efficiency?
- Thermal efficiency measures how effectively a boiler converts heat energy into steam or hot water.
- Combustion efficiency measures how completely fuel is burned in the combustion chamber.