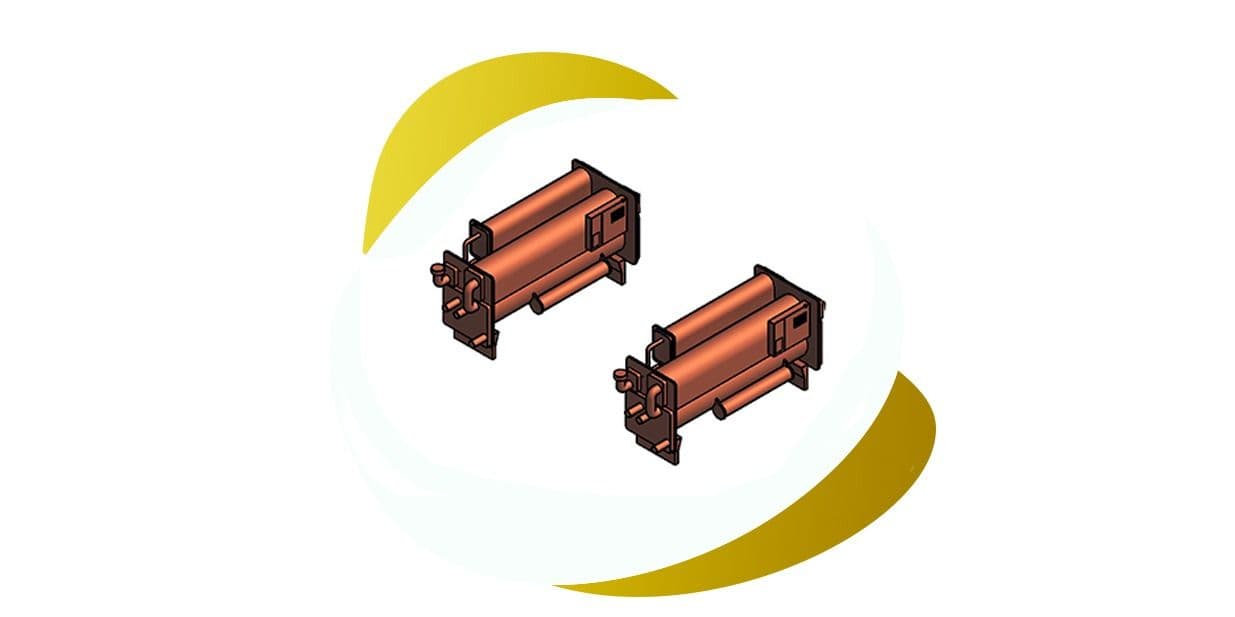
Testing and Validation of Absorption Chillers with Focus on Performance Per ASHRAE Standards
Introduction
'Green' building design and operation require integrating features that promote energy efficiency and sustainability. Heating Ventilating and Air Conditioning (HVAC) systems have evolved to become more energy efficient and environmentally friendly. As businesses look for ways to further cut down energy use and reduce carbon emission, new technologies for cooling have come into the limelight. One of these technologies is absorption chillers which offer energy efficient cooling by utilizing heat instead of electrical energy for the process. Absorption chillers are superior than vapour-compression chillers because they do not use mechanical compressors and instead use waste heat, hot water, steam or gas which can directly be fired. This makes the application of Absorption chillers useful in Industrial plants, Commercial buildings, Hospitals, and in conjunction with cogeneration plants.
It is equally important to note that Absorption chillers come with several advantages such as lower grid electricity requirements, decreased greenhouse gas emissions, decreased operational noise, etc. There is a caveat, however, when it comes to properly validating their operational performance, reliability, and efficiency. Operative conditions in which these machines function need special attention to ensure optimal performance. Standardized testing is important in verifying the reliability of the defined operational limits on these machines with respect to cooling capacity, energy efficiency, and effective requisite performance.
The American Society of Heating, Refrigerating, and Air-Conditioning Engineers (ASHRAE) created comprehensive standards for testing methodologies and validating performance criteria of absorption chillers. These include ASHRAE Standard 30-2019, concerning the testing of liquid-chilling packages, and ASHRAE Standard 90.1, which outlines minimum energy efficiency standards for buildings. Following these standards helps manufacturers and facility operators to ensure that absorption chillers deliver expected cooling capacity, efficiency, and environmental impact.
Understanding Absorption Chillers
What Are Absorption Chillers?
Absorption chillers are cooling devices that rely on heat rather than electricity to sustain the refrigeration cycle. In comparison to mechanical compression chillers which utilize electricity-driven compressors, absorption chillers are more suited for waste heat recovery or cogeneration applications, as they are powered by steam, hot water, or gas.
An absorption chiller relies on a cooling cycle which is driven by the interaction of a refrigerant-absorbent pair.
The two most commonly used working pairs include:
•Water-Lithium bromide (LiBr): used for large scale air conditioning systems
•Ammonia-water (NH3-H2O): used for industrial and low temperature cooling applications.
This process includes an essential set of steps:
1.Generator – Separates the refrigerant from the absorbent using heat.
2.Condenser – Changes refrigerant vapor back into a liquid.
3.Evaporator – Absorbs heat to produce a cooling effect.
4.Absorber – Redisolves the refrigerant vapor back into the absorbent solution.
Due to its low electricity consumption and reduced greenhouse gas emission, it is deemed to be an environmentally friendly and cost-effective solution for cooling in industries, hospitals, and commercial buildings.
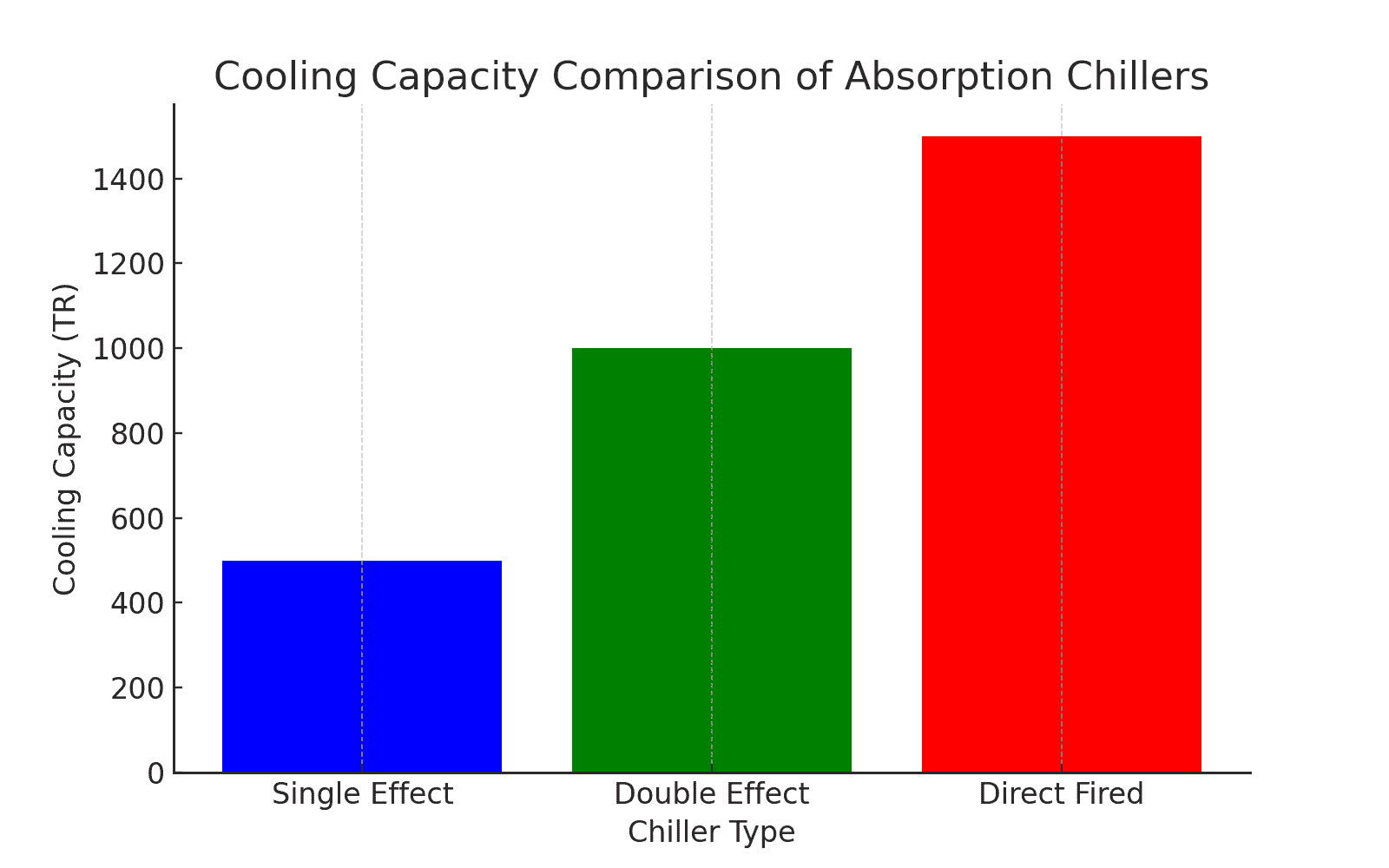
Advantages of Absorption Chillers
•High energy efficiency: uses waste heat or renewable energy.
•Environmentally friendly: employs refrigerants with low global warming potential (GWP).
•Quiet operation: fewer moving parts means less noise.
ASHRAE Standards for Performance Testing of Absorption Chillers
Overview of ASHRAE Standards
ASHRAE (the American Society of Heating, Refrigerating and Air-Conditioning Engineers) has made important performance testing standards to guarantee the effectiveness, dependability, and sustainability of HVAC units, including absorption chillers. Two significant ASHRAE standards that govern the performance evaluation of absorption chillers are:
1. ASHRAE Standard 30-2019: Methods of Testing Liquid-Chilling Packages – Defines procedures, test conditions and criteria for the performance of absorption chillers and other liquid chilling systems. This standard aims at operating efficiency of chillers over a range of operational scenarios.
2. ASHRAE Standard 90.1: Energy Standard for Buildings – Specifies the required minimum energy efficiency for buildings which include performance criteria for cooling systems like absorption chillers. It is useful for setting parameters for the environmentally sustainable HVAC operation.
The above ASHRAE standards enables manufacturers and building operators to verify the efficiency, cooling capacity, and energy expenditure of absorption chillers and confirm adherence to established industry standards.
Key Performance Indicators (KPIs)
ASHRAE governing guidelines specify a number of benchmarks concerning the efficiency of absorption chillers that need to be monitored and assessed:
1. Coefficient of Performance (COP) – The most basic criterion for measuring the level of energy efficiency an appliance has is its coefficient of performance (COP). It reflects the ratio of useful work obtained from the chilling device in the form of refrigeration to the heat energy supplied. The greater the COP, the more energy efficient the device is.
2. Cooling Capacity (Tons of Refrigeration) – Also known as the total cooling output, this metric is expressed in terms of kilowatts (kW) or tons of refrigeration (TR). The parameter indicates if the Appliance meets the cooling requirements needed by the building.
3. Heat Input Requirement – Determines the level of thermal energy that is wasted, especially in relation to the absorption process. The goal is to minimize heat utilization and energy waste during the process.
4. Part-Load Efficiency– Determines what happens to the performance of the chiller with different degrees of cooling load. As HVAC systems are not always running at full capacity, the part-load efficiency contributes significantly to energy savings.
5. Flow Rates & Pressure Drops – The movement across parts ( chilled water delivered to the building, cooling water coming to the chiller, refrigerants) of the Chiller is examined separately. Supplementary proper flow rates along with reduced pressure drops increase system efficiency.
6. Approach Temperatures – Analyzes the temperature differentials in heat exchangers to evaluate the efficiency of heat transfer. Better system effectiveness and stronger heat exchange performance is indicated with lower approach temperatures.
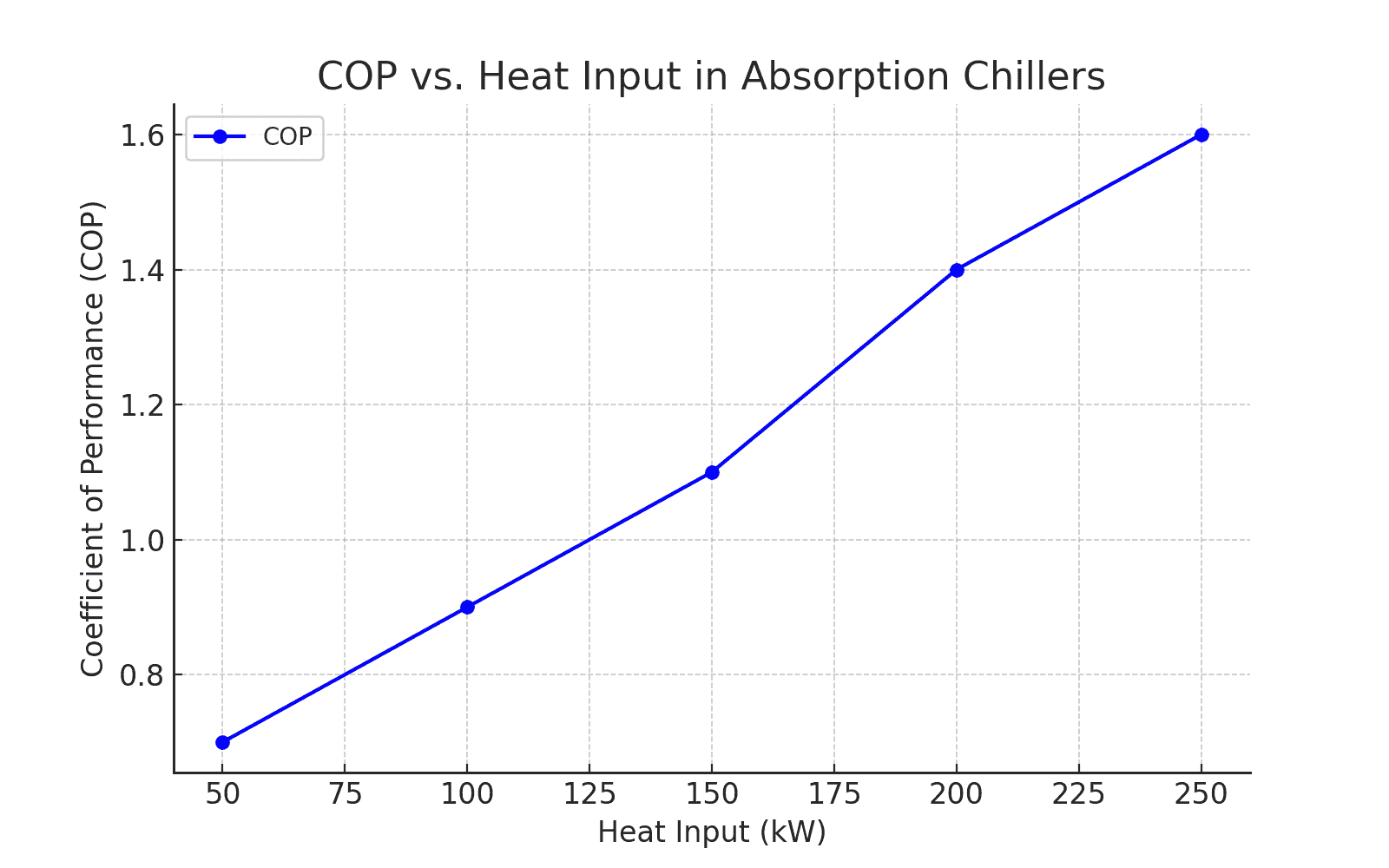
Testing Methodology on Performance
In order for absorption chillers to comply with ASHRAE, their performance testing needs to be thorough. The testing procedure is multi-step to ensure precision in efficiency and reliability during factory conditions, as well as in real-world conditions.
1. Factory Acceptance Testing (FAT)
– Takes place in the manufacturer’s facility before shipping.
– Ensure the chiller complies with design requirements, target cooling capacity and efficiency goals.
− Controlled testing environments assess COP, heat input, flow rates, and other relevant factors.
2. Site Performance Testing (SPT)
− Conducted post installation at the operating site.
− Validates actual performance across diverse environmental and operational scenarios.
− Integrates with BMS to assess efficiency at part-loads and other metrics.
3. Continuous Monitoring and IoT Integration
− Real-time data capture is done using smart sensors and IoT-embedded devices.
− Facilitates identification of performance change, inefficiencies, or maintenance issues.
− Enables predictive maintenance, thus minimizing downtime and operational expenditure.
Testing Absorption Chillers on Varying Conditions
According to ASHRAE, absorption chillers should be tested under the following conditions:
1. Steady-State Conditions - Reliable operation at fully loaded capacity has to be guaranteed.
2. Transient Conditions – Examines performance for scenarios dealing with particular and random load changes and disturbances.
ASHRAE’s standardized testing procedures allow organizations to have highly reliable absorption chillers that also meet efficiency benchmarks, leading to savings and minimal environmental damage.
Case Studies and Real Life Examples
Case Study 1: Gaining Value from Waste Heat at a Manufacturing Facility.
Location: Germany
Problem: Excessive energy expenditure and waste thermal energy from their industrial activities.
Solution: Installation of an absorption chiller using waste lithium bromide and double effect processes.
Results:
• A decrease of 35% in electricity use
• A 25% reduction in operational cost
• Reduced CO2 emission further improving the environmental rating
Case Study 2: A Medical Facility’s Focus on Enhancing Its HVAC System
Location: United States
Problem: Excessive reliance on grid electricity and cooling load for a medical facility.
Solution: Implemented tri-generation fuel cell (CCHP) with absorption chillers.
Results:
• Improved reliability of cooling for medically important areas.
• An improvement of 50% in energy efficiency.
• Savings in long term costs through smart energy use.
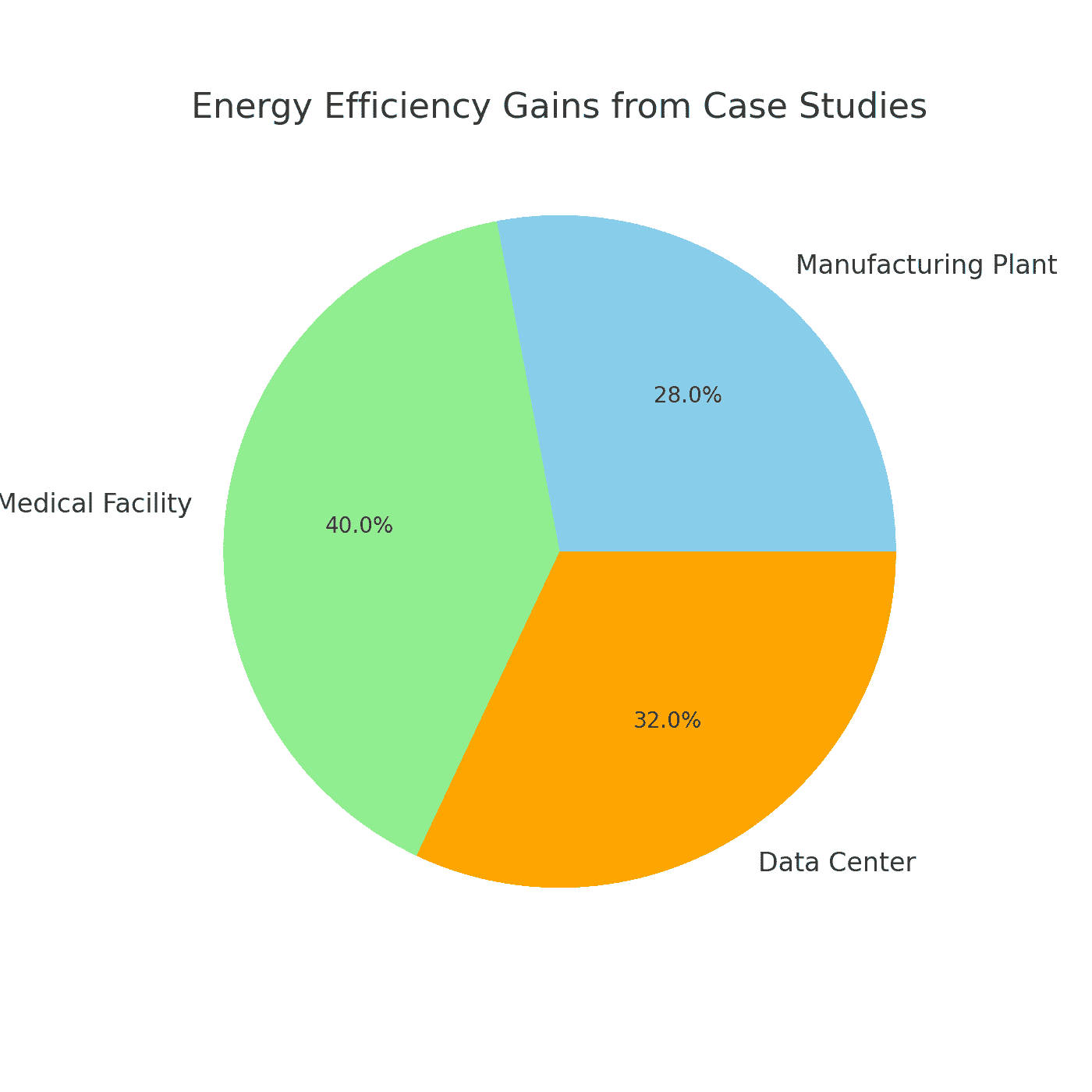
Insights and Future Trends
Latest developments with absorption chiller technology
• Hybrid Systems: Use of absorption and mechanical chillers in one system to improve efficiency.
• predictive maintenance using smart monitoring systems.
• New Refrigerants: Explore alternatives to low-GWP absorbents to further sustainability goals.
• Modular Designs: Integrated, compact, and scalable solutions for various commercial and industrial purposes.
Regulatory and Market Trends
• Energy Efficiency Mandates: Stricter HVAC energy consumption regulations are being set by governments.
• Green Building Certifications: Absorption chillers are highly rated by LEED and BREEAM due to their sustainable attributes.
• Increasing Adoption in Data Centers: Shifts toward heat driven absorption technologies for large cooling loads.
Conclusion
Compliance with ASHRAE standards on performance testing and validation of absorption chillers is crucial for optimal operation, energy efficiency, and sustainability of the system. Standardized practices allow industries to reap the benefits of implementing absorption chillers while minimizing the carbon emissions and cost in the long run. The future of absorption cooling integrates advanced monitoring, smart control technologies, and hybrid systems that position it as a key component in modern HVAC approaches.
With ongoing trends from businesses and other institutions towards cooling systems with energy efficient technologies, absorption chillers are emerging as the most dependable renewable solution that is cost effective for both commercial and industrial use. Organizations willing to validate the performance of their cooling systems find profound value in ASHRAE's extensive guidelines towards a sustainable energy aware future.
Frequently Asked Questions
What are absorption chillers, and in which ways do they differ from the traditional kind?
Absorption chillers operate through the use of heat instead of the electricity which drives traditional chillers, making them more environmentally-friendly and eco-efficient than mechanical compression chillers which rely on electric-watt powered compressors.
Why is ASHRAE compliance crucial with respect to absorption chillers?
With compliance to ASHRAE, absorption chillers can ensure accurate efficiency measures, performance, and the environment through sustainability benchmarks making it possible for industries to achieve optimal cooling while simultaneously using less energy and lowering emissions.
What are the feasibility and operation standards (KPIs) for absorption chillers?
The principal KPIs pertain to the Coefficient of Performance (COP), cooling capacity, heat input requirement, part-load efficiency, flow rates, pressure drops, approach temperatures to measure system efficiency, and effectiveness.
How is the absorption chillers’ performance tested and verified?
Performance validation includes factory acceptance testing (FAT), site performance testing (SPT), and real world efficiency and reliability check through continuous monitoring with IoT-based smart sensors.
What are the recent shifts in absorption chiller technology?
Shifts in focus include the adoption of modular structures, new low GWP refrigerants, predictive maintenance with IoT, hybrid systems that contain both absorption and mechanical chillers, along with increased usage within data centers for efficient cooling.