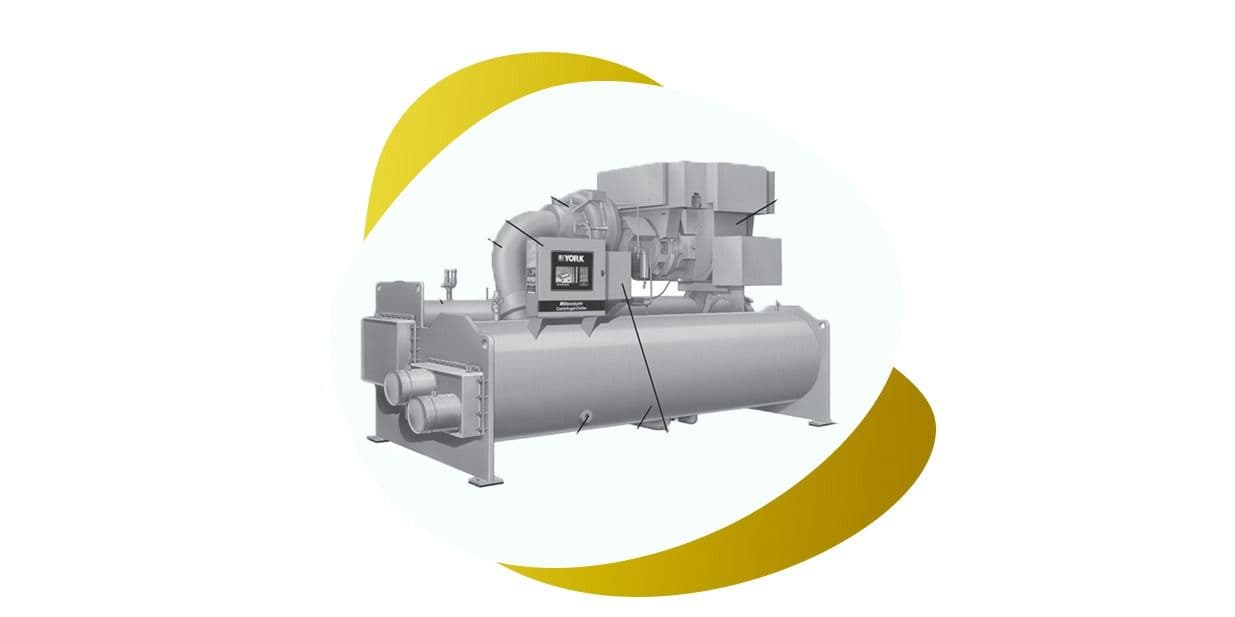
How to Optimize Your Centrifugal Chiller for Peak Performance?
If you manage a large commercial building, data center, or industrial facility, chances are a centrifugal chiller plays a major role in keeping things cool. These machines are the workhorses of HVAC systems, responsible for regulating indoor temperatures in vast spaces.
But here’s the thing—not all chillers run at their full potential. Many waste energy, overwork components, and cost more than they should simply because they’re not properly optimized.
So, how can you ensure your centrifugal chiller operates at peak performance, saving energy while delivering consistent cooling? Let’s dive into practical optimization strategies that will make your system more efficient, reliable, and cost-effective.
Why Centrifugal Chiller Optimization Matters
Before we get into the how-to, let’s answer the big question—why should you care about optimizing your chiller?
💰Lower Energy Costs: Chillers can consume over 50% of a building’s total energy, making efficiency improvements a big money-saver.
🛠Longer Equipment Life: A well-maintained chiller experiences less wear and tear, reducing the chances of breakdowns and expensive repairs.
🌍Eco-Friendly Operation: Efficient chillers use less energy, reducing carbon footprint and supporting green building initiatives.
🏢Consistent Cooling Performance: Nobody likes temperature fluctuations in office spaces, data centers, or hospitals. A properly optimized chiller ensures steady cooling.
Now that we’re on the same page, let’s get into the best strategies to optimize your centrifugal chiller.
1. Keep the Heat Exchanger Clean
The heat exchanger plays a crucial role in transferring heat efficiently. Over time, scale, dirt, and debris accumulate on its surfaces, reducing heat transfer and forcing the chiller to work harder than necessary.
How to Clean the Heat Exchanger for Better Efficiency:
✔Regular Inspections: Check for signs of scaling, corrosion, or fouling at least twice a year.
✔Tube Cleaning: Use mechanical brushes or chemical cleaning solutions to remove buildup.
✔Water Treatment Programs: Keep condensed water clean by implementing anti-corrosion and anti-fouling treatments.
A clean heat exchanger = improved efficiency and lower operating costs.
2. Optimize Chilled Water and Condenser Water Flow
Water flow plays a huge role in chiller performance. If the flow rate is too low or too high, the chiller becomes less efficient and may even experience premature failure.
Best Practices for Water Flow Optimization
🚰Maintain Proper Flow Rates: Follow the manufacturer’s recommendations for both chilled and condenser water flow rates.
🌡Monitor Temperature Differences (Delta T): The ideal temperature difference for chilled water should be 10°F to 14°F (5.5°C to 7.7°C) for maximum efficiency.
🛠Use Variable Frequency Drives (VFDs): Installing VFDs on pumps allows you to adjust water flow rates dynamically, based on cooling demand.
By controlling water flow properly, you ensure your chiller runs at peak efficiency without overworking the system.
3. Maintain the refrigerator Charge
Think of refrigeration as the lifeblood of your chiller. Too much or too little refrigerant can significantly impact performance and increase energy costs.
How to Keep Refrigerator Levels in Check:
🔍Monitor Pressure Readings: Too low or high pressure could indicate a leak or overcharge.
🛠Fix Leaks Immediately: Even a small refrigerant leak reduces cooling efficiency and harms the environment.
📊Ensure Proper Refrigerator Charge: Work with a certified HVAC technician to check levels and adjust if needed.
Proper refrigerant management ensures maximum cooling output with minimal energy consumption.
4. Use Advanced Controls & Automation
Manual chiller operation is a thing of the past. Advanced control systems and building automation allow chillers to adapt in real-time, reducing energy waste and improving efficiency.
Smart Ways to Automate Chiller Operations:
⚡Install Energy Management Systems (EMS): Automate chiller performance based on real-time cooling demand.
📈Use predictive analytics: AI-driven software can anticipate efficiency losses before they happen.
📊Integrate chillers with Building Management Systems (BMS): This ensures chillers run only when necessary, reducing unnecessary energy use.
The more intelligent your system, the more efficient your chiller will be.
5. Schedule Preventative Maintenance
A reactive approach to chiller maintenance (fixing things only when they break) is a costly mistake. Instead, adopt a preventative maintenance schedule to catch issues before they escalate.
Essential Chiller Maintenance Tips:
🔄performanceCheck compressor performance: inspect for excess vibration, unusual noises, and overheating.
🛠Clean and inspect Tubes: Dirt buildup reduces heat exchange efficiency.
🛑Test Electrical Connections: Loose connections can cause system failures and inefficiencies.
💧Monitor Water Quality: Poor water quality leads to scale and corrosion issues.
Regular maintenance can extend chiller life, reduce downtime, and maximize efficiency.
6. Upgrade to Energy-Efficient Components
Even the best-maintained chillers can benefit from modern upgrades. Technology has come a long way, and energy-efficient components can further enhance performance.
Top Chiller Upgrades to Consider:
⚡Variable Speed Drives (VSDs): Reduce compressor speed based on cooling demand, cutting energy consumption by up to 50%.
💡High-Efficiency Motors: Newer motors consume less power while delivering the same cooling output.
🌍Eco-Friendly Refrigerants: Switching to low-GWP refrigerants reduces environmental impact and improves efficiency.
Upgrading your chiller with modern components is an investment that pays off in energy savings and longer system life.
Final Thoughts: Is Your Chiller Operating at Peak Efficiency?
Optimizing your centrifugal chiller isn’t just about saving money—it’s about improving performance, extending lifespan, and reducing environmental impact.
Whether you’re managing a hospital, office building, or industrial facility, applying these best practices can drastically improve your chiller’s efficiency and lower operational costs.
So, when was the last time your chiller got a performance check-up? If you’re not sure, now’s the time to take action!
Frequently Asked Questions
1. Why is it important to keep the heat exchanger clean in a centrifugal chiller?
A clean heat exchanger ensures efficient heat transfer, which is crucial for the chiller's performance. Dirt, scale, or debris can accumulate over time, reducing heat transfer efficiency and forcing the chiller to work harder, which increases energy costs and wear on the system.
2. How does the refrigerant charge affect the performance of a centrifugal chiller?
The refrigerant charge must be maintained at the correct level for optimal performance. Too much or too little refrigerant can lead to inefficiencies, increased energy consumption, and potential damage to the chiller. Regular monitoring and prompt repair of leaks are essential.
3. What are the benefits of using advanced controls and automation for centrifugal chillers?
Advanced controls and automation, such as energy management systems and predictive analytics, allow chillers to operate more efficiently by adjusting to real-time cooling demands. This reduces energy waste, lowers operating costs, and can prevent efficiency losses before they occur.