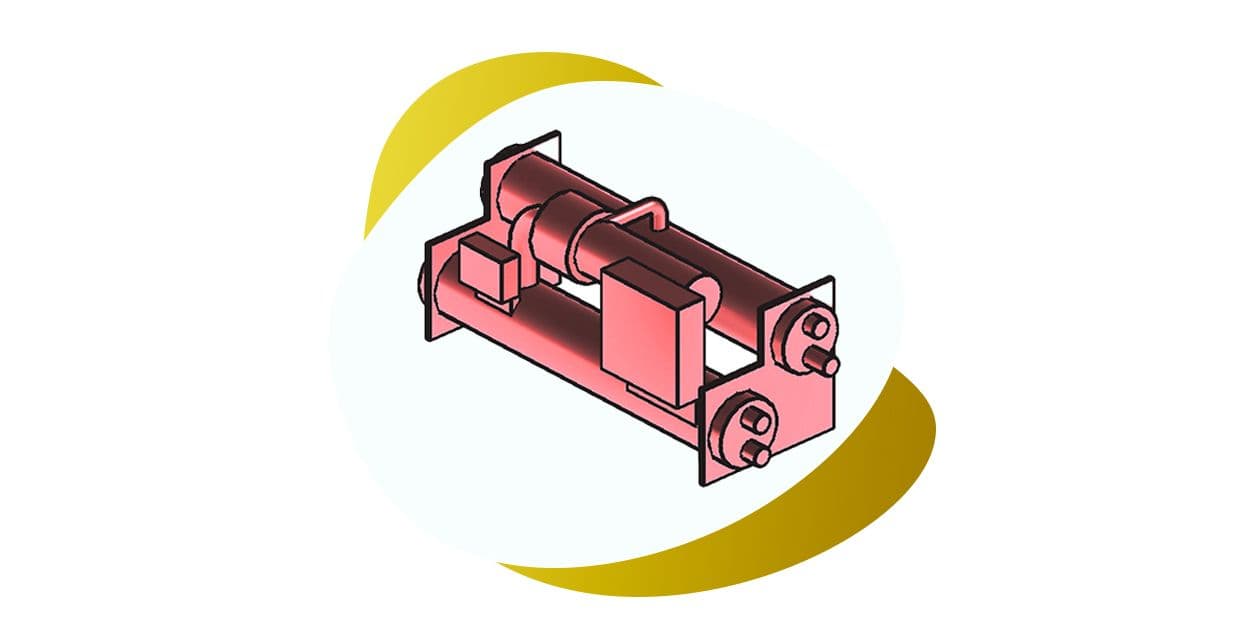
What is Centrifugal Chiller?
A Centrifugal Chiller is a type of water-cooled chiller that is used for large-scale air conditioning systems. It operates using a vapor-compression cycle. The coefficient of performance (COP) of a centrifugal chiller is higher as compared to other types of chillers that why they are very efficient .A centrifugal chiller consists of an evaporator, condenser, compressor, motor, lubrication system, graphic control center (OptiView), and all interconnecting unit piping and wiring.The main part of the centrifugal chiller was centrifugal compressor.
Centrifugal Compressor
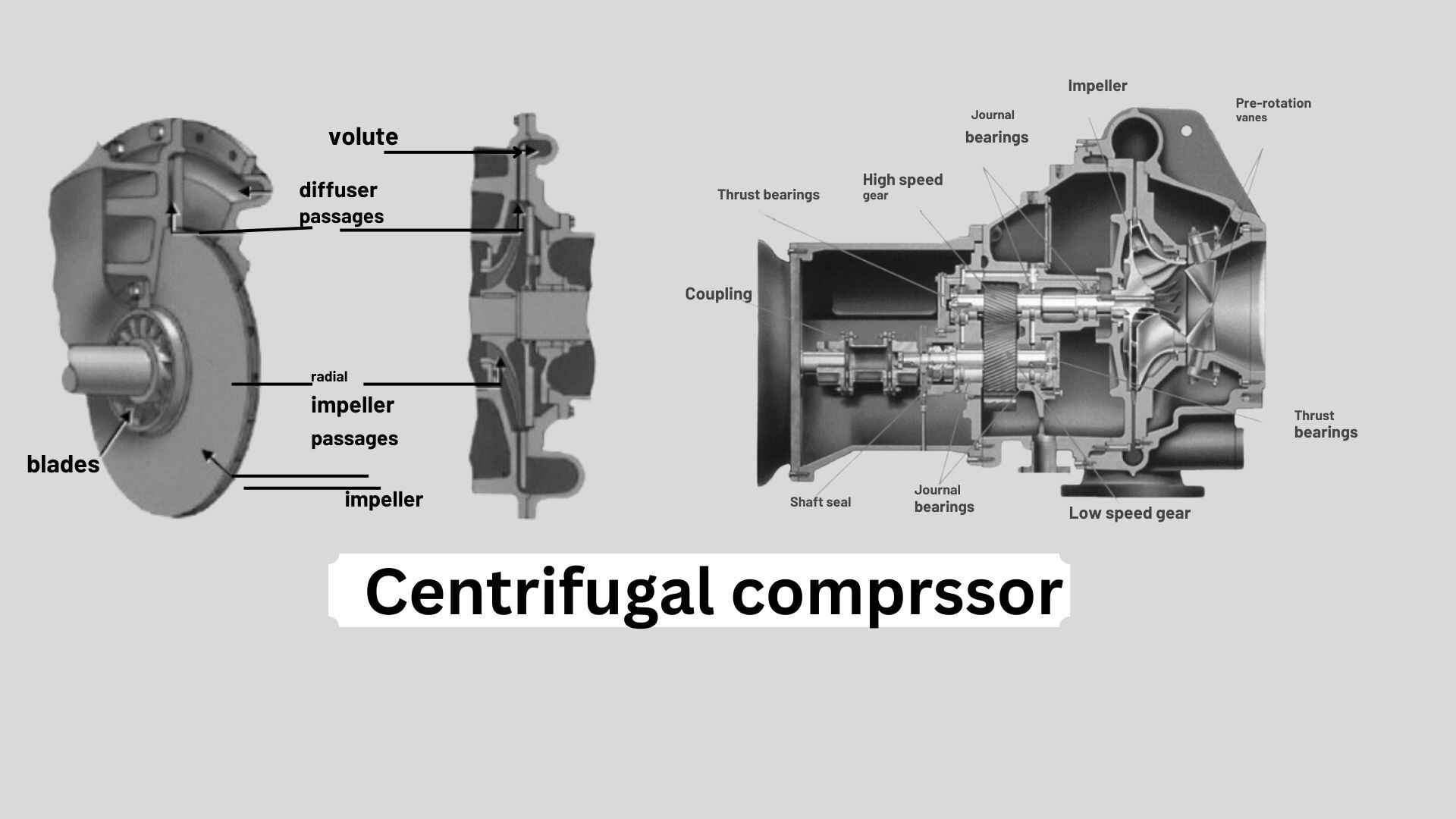
The Centrifugal compressor is a very important part of the chiller. Centrifugal compressor main job is to increase the pressure of the refrigerant, turning it into a hot, high-pressure gas. Centrifugal compressor type of compressor works with a spinning fan, called an impeller, to push and compress the refrigerant. It gets its power from an electric motor.
The Centrifugal compressor has several key parts.
Rotor
rotor is the spinning part that moves the refrigerant. It’s made of strong steel and includes a long metal rod (shaft) and the spinning fan (impeller). The impeller is carefully designed and tested to work smoothly and handle pressure evenly.
Bearings
bearings are small parts. bearing help the rotor spin smoothly and reduce friction. They are made of aluminum and support the spinning pieces.
Gears
gears take power from the motor and pass it to the impeller. gears are Arrange in a way that many teeth work together at the same time. which makes Gears strong and dependable. To keep everything running smoothly and avoid damage, An oil can is always held over the gears.
shaft seal
shaft seal stops refrigerant or oil from leaking where the spinning shaft meets the motor. It has two layers for extra protection and uses special materials to keep it working for a long time. The seal is always covered in oil to make sure it stays smooth and works well when the chiller is running.
Compressor Lubrication System
in compressor we use a lubrication system To keep the moving parts of a compressor running smoothly and to reduce friction, Just like in cars and other machines, lubrication helps minimize friction losses. Similarly, compressors also have a complete lubrication system. in compressor lubricate different parts, like gears ,shafts etc .
inside an oil tank, there's an oil pump (called an oil sump) . This pump circulates oil through the system to make sure everything runs smoothly.
When you press the START button, the oil pump starts and runs for 50 seconds to coat all the parts with oil. Then, the compressor motor starts. The oil pump keeps working the whole time the compressor is running and even for 150 seconds after it stops, to make sure all parts are properly lubricated.
The oil pump pulls oil from the oil tank. The oil goes through the oil cooler and in oil cooler heat is removed .Then, it passes through the oil filter to remove dirt.The clean oil moves to the emergency oil reservoir, which sends oil to all the compressor’s bearings and moving parts.The oil returns to the tank to be reused
When the chiller is not operating for a long time, the oil absorb refrigerant . The colder the oil gets, the more refrigerant it absorbs. If too much refrigerant mixes with the oil, it can cause problems when the system starts again.The mixture of oil and refrigerant goes into the reservoir, which has an oil heater. The refrigerant mixed with the oil is heated and turns into gas. This process helps separate the oil from the refrigerant
Compressor Motor
The part which powers the compressor is the compressor motor. The compressor motor is strong and reliable called a squirrel cage motor, built to work perfectly with the system. It spins at more than 2975 RPM; the compressor motor is designed to stay cool with air flowing through it. A sturdy iron support connects the motor to the compressor.
A metal flexible disc coupling connects the motor and the compressor. This coupling has a long life, does not wear out, and requires no oil or maintenance.
If the system uses a remote starter, there is a box provided to connect the wires. The motor’s wires are located inside this box, and special jumpers are included to help start the motor. However, wire connectors are not included. The system also has safety features to protect the motor if too much current flows through it.
If the system uses an optional Solid State Starter, check the options section for more information.
Graphic Control Center
The graphical control center acts as the brains of the system. It is installed and tested at the factory. This electronic panel automatically controls how the system works to meet cooling needs
condenser
The condenser is a very important part of the system. After the refrigerant is compressed in compressor and it is very hot and high pressure. This refrigerant gas goes into the of shell and tube heat exchanger called condenser . In the condenser, the hot refrigerant reject its heat to chilled water coming from a cooling tower. This chilled water absorbs the heat from the refrigerant, making the refrigerant cool down and change into a liquid again. After passing through the condenser, the refrigerant is high pressure but lower temperature compared to before. So, the main job of the condenser is to take the heat away from the refrigerant, using the cooler water from the cooling tower.
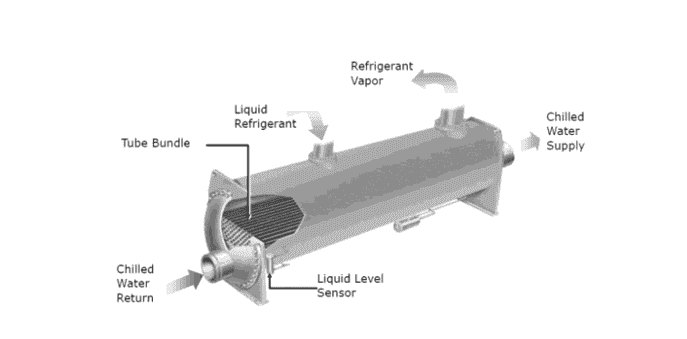
Evaporator
The evaporator is a also a shell and tube heat exchange in which Refrigerant absorb heat.
Inside the evaporator, the low-temperature, low-pressure refrigerant absorbs heat from the water coming from the AHU or FCU. On the side of the evaporator, there’s a small glass called a sight glass, with the help of sight glass you check the level of refrigerant inside the chiller and make sure it’s filled correctly. if the pressure of refrigerant inside evaporator gets too high then evaporator also has safety valves to release refrigerant
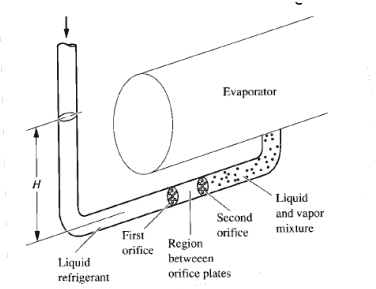
Capacity Control
A chiller is rated to process its full cooling power, but it doesn’t always need to operate at full capacity. It changes the amount of energy that it uses depending on how much cooling is required. The goal is to keep the chilled liquid at a required temperature as it flows out of the evaporator.
To make this happen, chillers use prerotation vanes (PRV). These are adjustable blades located at the entrance of the compressor, and their job is to control how much refrigerant flows through the system.
An electric motor takes care of adjusting these vanes automatically. The motor is connected to a lever arm outside the compressor, which opens or closes the vanes as needed. When the chiller is working at full power, the vanes are wide open. If less cooling is needed, the vanes close up.
Refrigerant Flow Control
The variable orifice regulates the refrigerant flow in the chiller. This analog signal is read by the chiller microprocessor, which uses a sensor to measure the refrigerant level within the condenser. The microprocessor knows at what level the refrigerant in the condenser (0%, it is empty; 100%, it is full) using this signal.
The microprocessor, in the response to this signal, modifies the variable orifice so as to keep the refrigerant level at a specified point (the aim level). Set points and other control settings help determine how sensitive and reactive the system will be. Only a qualified technician should set or change these parameters when the chiller is installed or at maintenance.
When chiller is in off state, that orifice would remain fully open, hence refrigerant level will be near empty. At startup of the chiller, the system verifies the refrigerant level is below the set point. If it is, the system slowly raises the level for roughly 15 minutes to get to the set point. If the level is already above the set point, it doesn’t ramp up the system; it immediately begins adjusting to maintain what’s set.
When the chiller operates, the refrigerant level is maintained at the set point. The control system only governs the level until a situation warrants an adjustment (i.e., vanes close), then the control system freezes level control until the vanes are reopened and changes the form that the system approaches the control point.
Options and Accessories
Service Isolation Valves
Certain chillers contain service isolation valves, which are unique valves. These are placed on the discharge and liquid lines. These valves should remain wide open as long as the chiller is operating. These valves are designed to isolate refrigerant either in the evaporator or in the condenser when servicing the unit. To safely remove the refrigerant for service, a refrigerant pump-out unit is required. Refrigerant isolation should only be performed by trained service technicians.
Hot Gas Bypass
Hot gas bypass, an optional feature, keeps the compressor from having issues when pressure is high or the load is light. Hot gas valve is open/closed through the chiller control panel. The valve must be adjusted by a trained technician using a special setup procedure. When the cold water flow varies, the HTG gas control valve is sequentially readjusted to ensure appropriate system operation.
Solid State Starter
The chiller also have optional features of solid-state starter. It assists in getting the motor running with less power, and keeps the inrush current stable as it ramps up. The starter is integrated into the chiller and is compatible with power systems of 380 and 600 volts. It features a protective box with a lockable door. They wire for power and controls at the factory, so it’s simple to install.
Variable Speed Drive (VSD)
Variable Speed Drive (VSD) allows the motor to be more efficient. The motor speed is varied and the vanes are positioned by it in terms of sensor readings.With a variable speed drive, the current in the motor is controlled. By controlling the current, the speed of the motor is also controlled. The main purpose of a variable frequency drive is to manage the flow of current in the motor It also assists the motor with the starting process, which in turn saves energy and cuts down on power usage. Also included is an optional harmonic filter that reduces electrical noise and enhances performance.
cooling needs while saving energy. It is pre-installed and tested at the factory.
Frequently Asked Questions
1. What is a centrifugal chiller?
A centrifugal chiller is a water-cooled system and centrifugal chillers was used in large air conditioning setups. It cools water using a vapor-compression cycle centrifugal chillers are very energy-efficient and ideal for big spaces like malls or office buildings.
2. What are the main parts of a centrifugal chiller?
The main parts are:
- Evaporator: Cools the liquid by removing heat.
- Condenser: Removes heat from the refrigerant using cooler water.
- Compressor: Increases the pressure of the refrigerant.
- Motor: Powers the compressor.
- Lubrication system: Keeps all moving parts smooth.
- Graphic control center: The “brain” of the system that ensures efficiency.
3. How does a centrifugal compressor work?
The compressor compress refrigerant with a impeller. It turns refrigerant into high-pressure and high Temperature , helping it circulate through the system. centrifugal compressor is powered by an electric motor.
4. Why does the lubrication system matter?
The lubrication system is like oil in a car—it reduces friction and keeps parts like bearings and gears running smoothly. It also has an emergency system to protect the compressor during power outages.
5. What does the condenser do?
in The condenser high-pressure and temperature refrigerant gas reject heat . It uses water from a cooling tower to remove heat, turning the refrigerant back into a liquid.