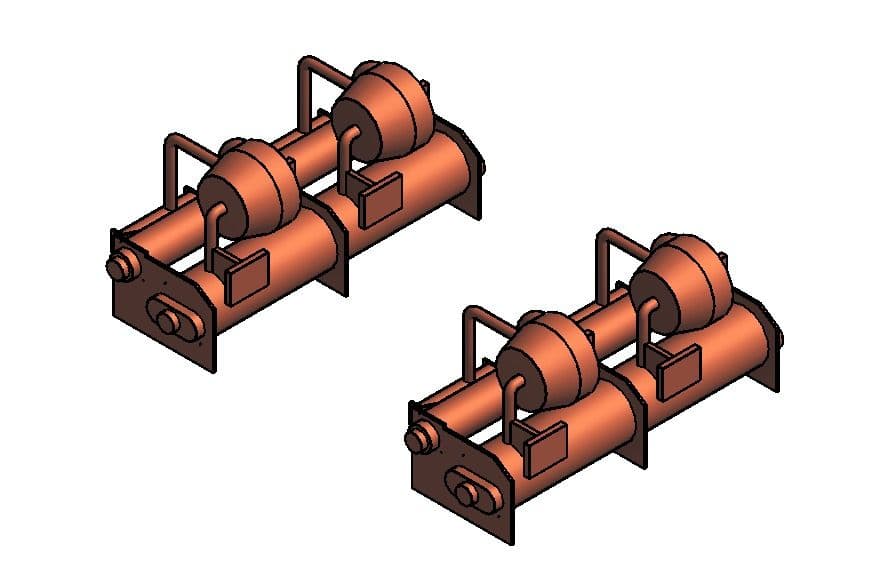
Chiller Compressors Unveiled: A Comprehensive Guide to Cooling Powerhouses in HVAC Systems
Chiller compressors are the driving force behind the HVAC systems that maintain comfort in large-scale environments, from towering skyscrapers to bustling hospitals. Chiller compressors are machines that compress refrigerant gas, enabling the heat transfer process that cools indoor spaces efficiently. However, with varying types, costs, and performance metrics, selecting the right chiller compressor requires a clear understanding of their capabilities and trade-offs. This guide explores the four primary chiller compressor types—reciprocating, screw, centrifugal, and scroll—detailing their mechanics, advantages, and ideal applications. Supported by industry data, visual aids, and practical insights, this article equips you with the knowledge to optimize your HVAC system’s performance.
What Is a Chiller Compressor?
A chiller compressor is the core component of a refrigeration system, responsible for compressing refrigerant gas to initiate the cooling process within the vapor compression cycle. This cycle consists of four key stages:
- Evaporation: The refrigerant absorbs indoor heat, transitioning from liquid to gas.
- Compression: The compressor increases the gas’s pressure and temperature.
- Condensation: The gas releases heat outdoors, condensing back into a liquid.
- Expansion: The liquid expands, reducing pressure and temperature, preparing for the next cycle.
Chillers are significant energy consumers, often accounting for up to 50% of a commercial building’s electricity use (U.S. Department of Energy, 2020). The compressor’s efficiency directly impacts operational costs, making its selection a critical decision. The four main types—reciprocating, screw, centrifugal, and scroll—each offer unique benefits tailored to specific needs.
Types of Chiller Compressors: A Technical Overview
Reciprocating Compressors
Reciprocating compressors operate using a piston-cylinder mechanism, akin to an internal combustion engine, where pistons compress refrigerant gas through reciprocating motion. They are versatile, with capacities ranging from 0.5 to 150 tons, making them suitable for small commercial spaces like retail stores or offices. Efficiency, measured by COP, is 4.2–5.5, but research suggests they lose approximately 25% more energy than scroll compressors due to frictional losses (Sunrise Metal, 2022). Noise levels are 70–80 dBA, comparable to heavy traffic, which may require sound insulation in noise-sensitive environments.
Maintenance is high due to multiple moving parts, including pistons and valves, necessitating frequent checks and replacements. The initial cost is low, with a lifespan of about 15 years. A key feature is multi-staging, allowing sequential cylinder activation for capacity control, enhancing flexibility for varying loads.
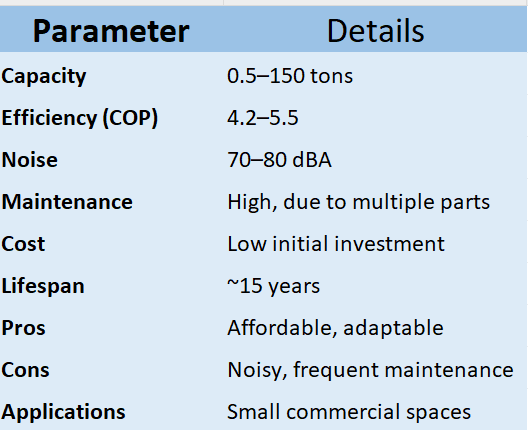
Screw Compressors
Screw compressors use two interlocking helical rotors to compress refrigerant continuously, offering smooth and quiet performance. They are ideal for mid-to-large facilities like schools or warehouses, with capacities from 70 to 750 tons. Efficiency varies by cooling type, with air-cooled systems achieving a COP of 2.9–4.15 and water-cooled systems reaching 4.7–6.07, suggesting water-cooled options are more efficient due to better heat dissipation. Noise levels are 60–70 dBA, akin to a conversation, enhancing suitability for noise-sensitive environments.
Maintenance is low due to fewer moving parts, though oil is required for lubrication and sealing, necessitating periodic checks. The upfront cost is high, but operational costs are lower, with a lifespan of approximately 25 years. Technical features include a slide valve for capacity modulation and variable speed drives (VSDs), which can boost efficiency by up to 18%, as seen in Ingersoll Rand’s R-Series (Ingersoll Rand, 2023).
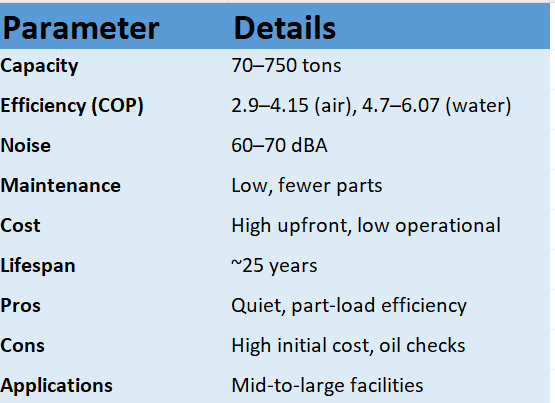
Centrifugal Compressors
Centrifugal compressors use a rotating impeller to accelerate refrigerant, converting kinetic energy into pressure via a diffuser, ideal for large-scale cooling. They handle capacities from 200 to 1,000+ tons, suitable for high-rise buildings, data centers, and hospitals. Efficiency is exceptional, with COPs of 5.8–7.1 for water-cooled systems, making them cost-effective long-term. Noise levels are 70–80 dBA, requiring potential sound insulation.
Maintenance is medium, focused on the impeller and bearings. The upfront cost is very high, but they offer durability with a 25-year lifespan. A challenge is surge, where airflow reverses at low loads, destabilizing the system. Modern VSDs and inlet guide vanes mitigate this, improving efficiency by up to 50% since the 1990s (U.S. Department of Energy, 2020).
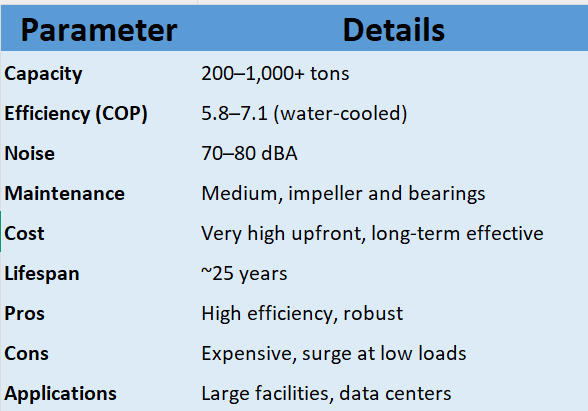
Scroll Compressors
Scroll compressors feature two spiral disks—one fixed, one orbiting—that compress refrigerant with minimal friction, making them quiet and efficient for smaller systems. They handle up to 30 tons, ideal for server rooms, small offices, or residential units. Efficiency ranges from a COP of 3.2–4.86 (air-cooled) to 4.45–6.2 (water-cooled). Noise levels are 48–60 dBA, akin to a refrigerator, enhancing suitability for noise-sensitive environments.
Maintenance is low, often hermetically sealed, with a lifespan of about 15 years. The upfront cost is moderate, and they are 25% more efficient than reciprocating units (Sunrise Metal, 2022). A compliance mechanism allows scroll separation if liquid enters, preventing damage, though capacity is limited by a fixed compression ratio.
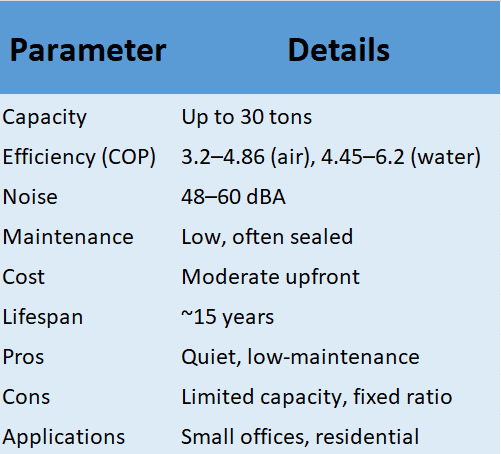
Choosing the Right Compressor: A Practical Guide
Selecting a compressor involves balancing several factors:
1. Cooling Load:
- <100 tons: Reciprocating or scroll.
- 100–200 tons: Screw or multiple reciprocating units.
- 200 tons: Screw or centrifugal.
2. Load Variability:
- Variable loads: Screw with VSDs excels at part-load (high IPLV).
- Steady, high loads: Centrifugal maximizes full-load efficiency.
3. Budget:
- Limited funds: Reciprocating.
- Long-term focus: Screw or centrifugal for energy savings.
4. Noise:
- Sensitive areas: Scroll or screw (<70 dBA).
5. Maintenance:
- Minimal upkeep: Screw or scroll.
Case Study: A Miami hotel upgraded from a reciprocating to a screw compressor, cutting energy use by 20% and resolving noise complaints, with the investment recouped in five years.
Economic Considerations
- Initial Cost: Reciprocating is cheapest; centrifugal is priciest.
- Operating Cost: Centrifugal achieves 0.5–0.6 kW/ton at full load; screw optimizes part-load via IPLV.
- Maintenance: Reciprocating demands frequent repairs; screw and centrifugal are less intensive.
- Lifespan: Screw and centrifugal last 25 years, outpacing others.
Leading Brands
- Reciprocating: Copeland, Carrier—cost-effective reliability.
- Screw: Trane (Adaptive Control), York—part-load innovators.
- Centrifugal: Carrier (AquaEdge), Daikin—large-system leaders.
- Scroll: Danfoss, Copeland—quiet efficiency.
Conclusion
Chiller compressors are pivotal to HVAC performance, balancing efficiency, cost, and durability. Reciprocating suits small, budget-conscious setups; screw excels in mid-to-large applications; centrifugal powers massive systems; and scroll thrives in quiet, compact spaces. With this guide, you’re equipped to make an informed choice, ensuring optimal cooling and cost efficiency.
Frequently Asked Questions
1. What is the primary function of a chiller compressor in an HVAC system?
A chiller compressor compresses refrigerant gas, initiating the vapor compression cycle that absorbs indoor heat and releases it outdoors. This process is essential for cooling large commercial buildings, hospitals, and industrial facilities efficiently.
2. How do different types of chiller compressors compare in efficiency and application?
- Reciprocating: Best for small commercial spaces; lower efficiency but cost-effective.
- Screw: Ideal for mid-to-large buildings with variable cooling needs; offers high part-load efficiency.
- Centrifugal: Most efficient for large-scale cooling in skyscrapers and data centers; has a high initial cost but lower long-term expenses.
- Scroll: Suitable for small offices or server rooms; quiet and low maintenance.
3. What factors should be considered when choosing a chiller compressor?
Key considerations include:
- Cooling Load: Smaller loads (<100 tons) use reciprocating or scroll, while large loads (>200 tons) benefit from screw or centrifugal.
- Load Variability: Screw compressors handle variable loads well, while centrifugal works best for steady, high loads.
- Budget: Reciprocating units have the lowest upfront cost, while centrifugal offers the best long-term savings.
- Noise Sensitivity: Scroll and screw compressors operate quieter than reciprocating or centrifugal models.